-
-
Air Compressor
A machine that compresses air to be used for blowing, pneumatic machines, sandblasting, or to cool you off a little. NEVER EVER take the blower end of the machine and stick it up someone's butt. It may sound like a great prank, but that air pressure can kill someone. Don't do it.
Back to Top
Alien Skin
This is a very neat technique we love here at Elev8 Premier. There are a lot of names for this. Its a form of bubble trap, sleeving and fuming. What is alien skin to us - WOW is how this makes us feel when we see it, so it must be out of this world. How it sometimes made is a dark tube, maybe jet black is used. Sometimes a blower will make their won coil pot tube. Once the blower has the colored tube they will roll it on a frog or take a knife and put lines into it. Then the blower will fume the glass with silver and or gold. We prefer to get that perfect fume of silver mixed with gold to get that amazing green color. Once you have this the blower takes it and puts it inside a clear tube of glass and then removes the air around it. This traps small air bubbles in the glass, hence why we call it bubble trap also.
Back to Top
Amphora
This is a tall ancient Greek or Roman jar with two handles and a narrow neck. Glass blowers use the term to refer to a classical vase design.
Back to Top
Annealer (Kiln)-
Glass works made from glass that have been super heated need to cool very slowly down to room temperature. If it cools too fast the glass will get stresses and it will crack. These machines are large ovens or kilns used to slowly cool the glass very slowly down to room temperature.
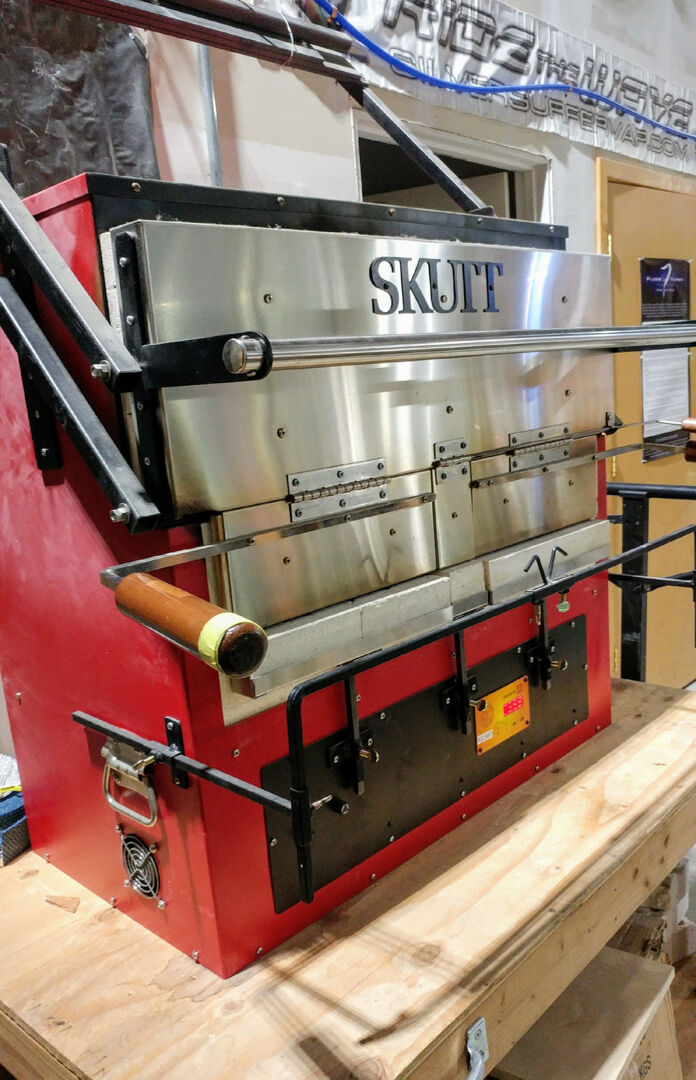
Back to Top
Annealing-
The process of letting the glass cool very slowly so that internal stresses are removed and the glass is tougher than it was. What annealing is to us as glassblowers- This can mean a lot of things to us in the glass blowing world, yet still means the same thing. We anneal the glass in order to remove the stress. The stress is built up in the glass as some parts are hotter than others and the molecules move differently depending on if they were hotter or cooler. What we are doing when we anneal is to bring all the molecules up to the same temperature so they all dance the same. This is not actually annealing though. The annealing starts as we cool the glass. The slower the better. This allows all the molecules to cool at the same rate. This way the molecules arrange in a more uniform way. The thicker the glass the slower the glass much cool to become fully annealed. Borosilicate glass anneals at 1050 F. Soft glass (Moretti) anneals at 960 F.
Borosilicate Ramp up - 38 min ambient to 1050F
Soak - 15 min at 1050F
Slow Cool - 30 min to 910F
Fast Cool - 47 min to ambient
|
Soft Glass Ramp up – 3 hours ambient to 960F
Soak – 1 hour 30 minutes at 960F
Slow Cool – 2 hours to 810F
Fast Cool – 1 hour to ambient
|
Borosilicate Annealing Chart
THICKNESS (INCHES)
|
0.125
|
0.25
|
0.50
|
0.75
|
1.00
|
2.00
|
3.00
|
4.00
|
5.00
|
6.00
|
Hrs @ A/T
|
0.5
|
1
|
2
|
3
|
4
|
8
|
12
|
16
|
20
|
24
|
Hrs @ A/T – 125 deg
|
0.2
|
0.5
|
1.7
|
3.2
|
4.5
|
10
|
21
|
38
|
60
|
85
|
Hrs @ A/T – 200 deg
|
0.1
|
0.2
|
0.5
|
0.8
|
1
|
1.5
|
3
|
5
|
8
|
11
|
Hrs @ A/T – 350 deg
|
0.2
|
0.3
|
0.5
|
0.5
|
1
|
1
|
2
|
4
|
7
|
10
|
Hrs @ A/T – 550 deg
|
0.25
|
0.25
|
0.3
|
0.5
|
0.75
|
1
|
2
|
4
|
5
|
10
|
Total Hrs
|
1.25
|
2.25
|
5.0
|
8.0
|
11.25
|
21.5
|
40
|
67
|
100
|
140
|
Anneal Time: 1 hour for every 0.25 inches of piece thickness
Soak Time @ A/T – 125 deg: 50% of the Anneal Time for pieces 0.25 inches thick or less. 100% of the anneal time for pieces greater the 0.25 inches thick
Soak Time @ A/T – 200 deg: 25% of the Anneal Time
Soak Time @ A/T – 350 deg: 25% of the Anneal Time
Soak Time @ A/T – 550 deg: 25% of the Anneal Time All temperatures are in degrees F and for 33 expansion borosilicate glass.
A/T = Annealing Temperature.
Critical temperatures for clear:
- Working temperature: 2228 degrees F
- Softening temperature: 1508 degrees F
- Annealing temperature: 1050 degrees F
- Strain temperature: 960 degrees F
For closed vessels, assume the wall thickness to be doubled (i.e. 0.125 wall = 0.5 wall for annealing, 0.5 wall = 1.0 wall, etc.).
An art glass piece may also be brought to temperatures 100 to 150 degrees above the A/T for a few minutes to improve the vibrancy of certain colors. This does not improve the annealing process.
As the wall thickness increases, the first soak stage (the soak time at the first temperature drop equal to the A/T minus 125 degrees), becomes more critical in the overall annealing process. This temperature is just below the strain point and allows the thicker, more complex pieces to cool slowly and come to a steady state before continuing with the ramp down in temperature. Additional soak points allow the piece to cool in a controlled fashion and to stabilize before continuing the cooling process.
The times listed for each of the soak periods includes the ramp downtime as well as the time at the new temperature for holding. For example, for a one-inch thick piece, the time at the A/T is approximately 4 hrs. After 4 hrs, reduce the temperature by 125 degrees and allow the piece to soak for another 4 hrs. Then reduce the temperature again for a 1-hour soak, etc.
The annealing schedule is based on clear boro glass and may need to be adjusted for the different colors being used. Specifically, metallic based colors may need a slightly higher A/T (maybe 25 degrees). The magnitude of the temperature decrease may need to be adjusted as well. The soak times can also be a variable that can be adjusted by color in conjunction or separately with the ramp down temperatures.
For non-metallic colors, the soak duration may be able to be reduced and the last one to two ramps eliminated altogether. For pieces that are to be re-worked, it may be necessary to ramp up the temperature of the piece in reverse order to avoid cracking.
The thought is that a piece that can crack during the annealing and cooling process might also crack during re-heating.
While having compatible COE’s between the different colors and the clear tubing and rod is of primary importance, similar annealing characteristics of the different glass components are also something that needs to be considered. If the annealing temperatures are different enough, and the cycle is set for a component with a lower annealing temperature, the higher end component(s) may not be fully annealed and therefore there may be enough residual stress to cause the piece to check either during cooling or at some later date.
Colors like Forest Green, Moss, and Blue Spruce all have annealed and strain temperatures approximately 100 degrees lower than either the clear or the other standard colors. This is by design and is accomplished in the formulation process. The softening point of these colors is still the same (approximately 1508) so there will not be any piece deformity even though annealing is occurring 100 degrees above the A/T. These colors were prone to cracking before the re-formulations about 18 months ago and one of the objectives was to make them more “annealing friendly”.
In general, the assumption built into the schedule is that even if the COE’s of the clear and different colors are compatible, the annealing temperatures may not be. If this is the case, care must be taken to minimize/eliminate the possibility of cracking by increasing the different soak times and decreasing the temperature drops between each soak. An additional soak period may also be necessary with some colors.
Other factors that can increase or require changes to the annealing cycle include:
- How complex the piece is and the number of sharp angles (sculptural induced stresses)
- What the thickness variation within the piece
- Thermal gradients in the annealing kiln itself (larger kilns suffer from this more)
- The absorption characteristics of the colors used (variation in the absorption of light in the different spectrums and how this affects radiant cooling/heating rates)
- The amount of re-work and extended heating and cooling
Back to Top
Atmosphere-
This refers to the conditions within the torch flame. The atmosphere can be described as oxidizing (High in Oxygen) or reducing (Low in Oxygen).
Oxidizing Flame - is the flame produced when an excessive amount of oxygen is used. When the amount of oxygen increases, the flame shortens, its color darkens, and it begins to hiss and roar. As its name suggests, it oxidizes the glass surface. Some glass colors love to be worked in this flame and others do not. Reducing Flame - is the flame with low oxygen. It has a yellow or yellowish color due to carbon or hydrocarbons which bind with (or reduce ) the oxygen contained in the materials processed with the flame. [1] The reducing flame is also called the carbonizing flame . This is a much cooler flame and some colored glasses love to be worked in this flame.
Back to Top
Aventurine-
Special glass that is made with flecks of copper. The copper adds a bit of sparkle to the Venetian style of work and ups the cost to make the glass. Northstar makes a color called Mystery Aventurine.
Back to Top
Avolio-
Hourglass shaped connecting piece commonly seen in Venetian style goblets. The avolio serves as not only a visual element, but also provides a thin spot which makes it easier to use the fork to load the goblet into the kiln. 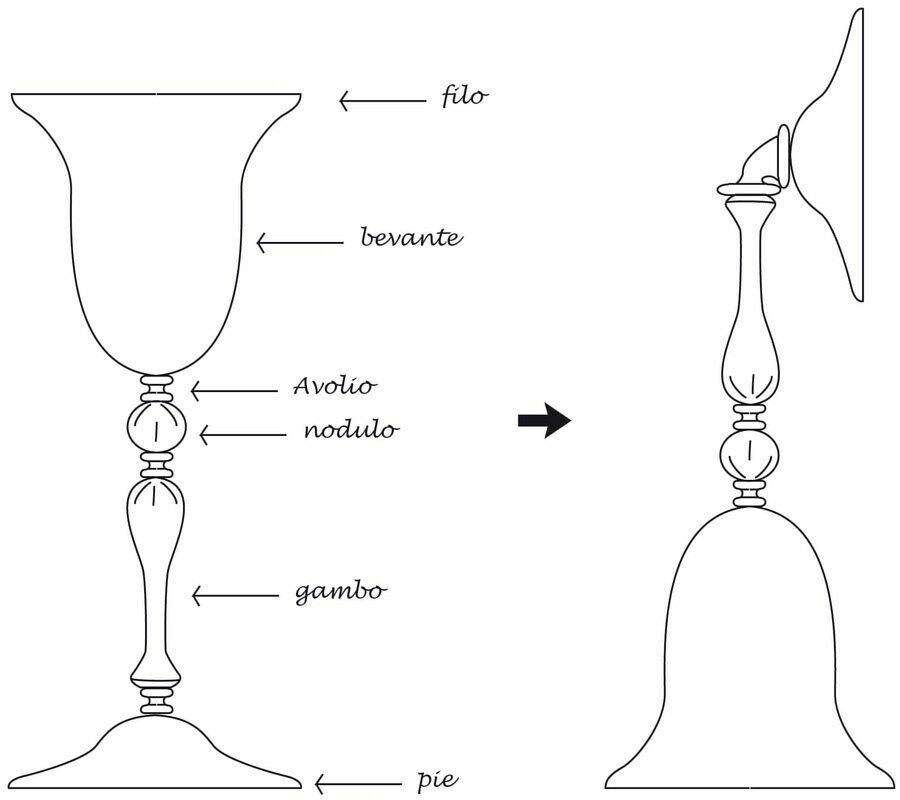
Back to Top
Batch-
Batch is the raw materials that are melted into glass. The process of melting batch is called charging and is quite time-consuming; our furnace requires about 9 hours to cook the batch until it is relatively bubble-free. Borosilicate can take up to 3 days to get bubble free.
Back to Top
Bead Release-
Usually, this is a consistency of mud. Used to put on mandrels so that the glass can be taken off of the metal rod (mandrel). Once it is on the rod it is dried so it is hard and the glass can be layered on top of it.
Back to Top
Blank-
A blank is a small hollow glass cylinder made using a specific color technique. Several blanks can be made from one large bubble, then each blank can be used to make a single piece. The white striped blank is used for making mezzo-filigree.
Back to Top
Bleb-
A bleb is that little bit of glass left on the end of the tube when you split a tube or take the glass off when you close the end. This can be removed with a glass rod to make the wall thickness evener. The bleb will cause the glass to gather in that spot if not removed.
Back to Top
Blow Hose-
A hose that a blower hooks one end up to a tube of glass and then the other end goes in their mouth. The blower will use this to blow air into the glass to pop a hole, to keep the glass shaped or to blow the glass larger when heated.
Back to Top
Blow Hose Assembly -
This is the blow hose, swivel and mouthpiece all assembled as one unit. These pieces work better as a group then by themselves.
Back to Top
Billow-
This is where the tube of glass shrinks or condenses in. 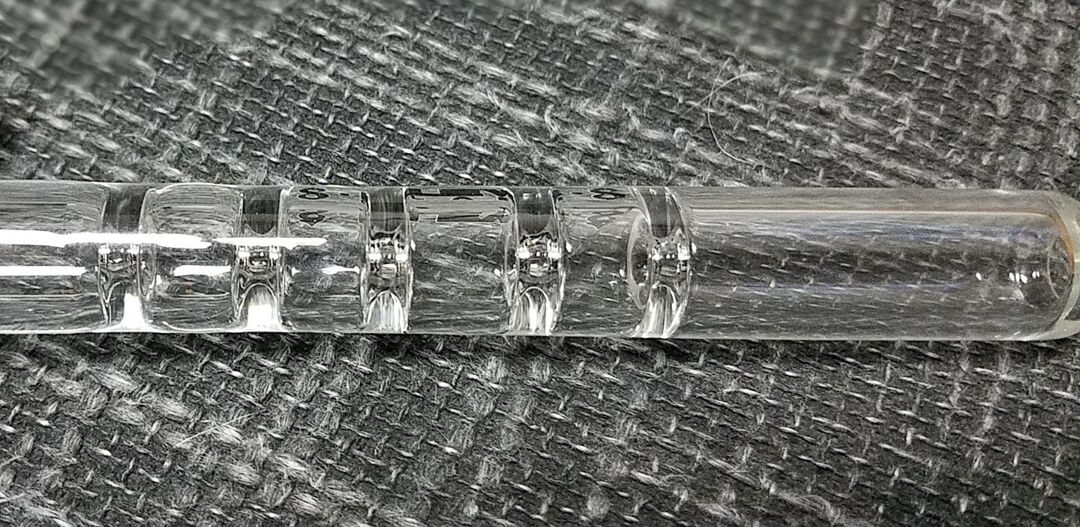
Back to Top
Body Wrap-
A body wrap is a single thread of glass that is applied to the outside of a vessel. It is very difficult to put one of these on and have it line up properly.
Back to Top
Bong (Waterpipe or Dab Rig)-
Glass water pipes offer a traditional method for smoking herbs. Similar to the design of a hookah but more compact and portable for mostly one person at a time to use. These types of water filters feature an air-tight water vessel with a bowl or adapter for loading herb or hooking up to a vaporizer. Most have a downstem in them as the first water diffuser. Each inhale bubbles up through the water, purified and cooled. While glass water pipes come in a variety of shapes and sizes, the essential function of delivering smoother, cooler, and cleaner hits is the same across the board. The main point of a water filter pipe is to purify, moisturize, and cool the smoke or vapor before it reaches your lungs, making for a much more comfortable and enjoyable experience.
For those who prefer concentrates, dab rigs are really the only way to fully enjoy the experience. With bangers operating at higher temperatures than vaporizer users will feel the burn of the dab, being greatly reduced when used in a dab rig.
There are 3 basic shapes to a bong:
Beaker Bong
This style is our favorite. The base is very sturdy as well as the glass is thick for the joint weld.
Bubble Bong
This is a great style, but what we find is that many times, if not made properly the glass, can get a little thing. Also, many times the beaker has a much wider base, so there is less chance of tipping over.
Straight Tube Bong
This is a great tube for being sturdy, much like a beaker bong. What we do not like about this style is 80% of the water pipes we see that are straight tubes are very thin at the joint weld. This is due to the fact that you must blow a bubble to get the right angle. This causes the glass to get thinner than the rest of the glass in this area. Over the years the bases have also gotten much thicker and good manufacturers have figured how to make the weld thicker by the joint. Always look at this joint weld when looking at a straight tube bong.
Back to Top
Borosilicate Glass-
A type of glass with silica and boron-trioxide as the main glass-forming constituents. Borosilicate glasses are known for having very low coefficients of thermal expansion (~3 × 10 −6 K −1 at 20 °C), making them resistant to thermal shock, more so than any other common glass. Such glass is less subject to thermal stress and is commonly used for the construction of reagent bottles In addition to quartz, sodium carbonate, and aluminum oxide traditionally used in glass making, boron is used in the manufacture of borosilicate glass. The composition of low-expansion borosilicate glass, such as those laboratory glasses mentioned above, is approximately 80% silica, 13% boric oxide, 4% sodium oxide and 2–3% aluminum oxide. Though more difficult to make than traditional glass due to the high melting temperature required, it is economical to produce. Its superior durability, chemical and heat resistance finds use in chemical laboratory equipment, cookware, lighting, and in certain kinds of windows. “The softening point (the temperature at which viscosity is approximately 107.6 poise) of type 7740 Pyrex is 820 °C ( 1,510 °F ). Borosilicate glass is less dense (about 2.23 g/cm3) than typical soda-lime glass due to the low atomic mass of boron.”
Back to Top
Bowl-
A bowl refers to the top part of a goblet, the part that you drink from. There are many different shapes for bowls, used for different kinds of drinks.
Back to Top
Bowl Push-
This tool is used by a blower to make their bowl in a pipe. Some blowers have 3-5 of them. You can make them or buy them. They can be made of graphite or brass.
Back to Top
Bubble Trap-
The bubble trap technique is when the glassblowing artist traps bubbles in the glass. When done properly the bubbles can form lines and can look very nice. Sometimes the bubbles are put in between ratachello line work. Bubble trap can be done in many ways. The blower can push dents into the glass and then put glass on top of that dent making a bubble. The can also use a frog to get a bunch of dents in a pattern, or they can sleeve glass with dents to get bubbles. A glass artist can also use stringers and the sleeving technique to trap air.

Back to Top
Bucket (Water Bowl) -
The bucket is where our hopes and dreams go on the bad days. Sometimes just a metal bucket and sometimes a metal bowl filled with water.
Water bowl - At our studio, we use the water bowl as our main bucket. Then we dump this bowl of the broken glass contents into our larger trash bucket when we clean our stations. The water bowl is used to put hot glass in so it cools off very fast. You must be careful here not to put in too big of a piece of glass that is too hot. There is a lot of energy in this glass and as it cools in the water it pops and explodes, so be careful not to put too big a piece of glass in your water bowl. The water bowl is also used as a shocker to shock a piece of glass rod you use to rip off trash glass. Simply put the hot glass in the bowl, it will crack and pop, then hit the edge of the bowl and your trash will pop off the glass rod. The water bowl works best as a tool when you have it filled to about 1/2" to 1" from the top.
Back to Top
Burner
The heat source of the flameworker. It usually runs on gas and oxygen or air. It consists of a head that contains many orifices to distribute and direct the flame, a body where the gas is passed up to the head, and a valve assembly where the proportions of the gas/oxygen mix and volume are controlled.
Back to Top
Calipers -
A device used to measure the distance between two opposite sides of an object. A caliper can be as simple as a compass with inward or outward-facing points.
Back to Top
Casing-
The application of one layer of glass over another, usually to achieve a layered effect for graal or cameo glass.
Back to Top
Chucks -
This is the part of the lathe that grasps the glass. There are basically two kinds. There is the scroll check that uses a key to open and close it. Then there is a planetary chuck that uses a plate on the check to open and close the chuck.
Back to Top
Claw Tool Holder (Grabbers) -
A device used to hold hot glass.
Standard Claw Tool -
This tool is used to hold say glasses, bases to glass, larger marbles or nearly anything you need to hold that you can not hold with your hand or that you do not want to use a punty to hold the glass with. A standard claw tool is usually made of a handle that has 6-8 hardened wires pressed into it. Then there is a slip ring with a threaded lock on it to hold the wires in place around the hot glass.
Marble Claw Tool -
This tool is slightly different than the standard tool in that the ends are bent in a circle to hold a marble better without it dropping out and edge.
Back to Top
Coefficient of Expansion-
The relative amount that a material will expand when heated.
Back to Top
Coil Pot-
This is an old school technique a blower uses to make their own tubing. Usually made on a blow tube with a colored stick of glass. Coil Pot by a blower - What you do here is get a blow tube, we usually use a 12mm tube. Flare the end open and then get you some of your favorite colored rod of glass. Heat this rod up and when it becomes hot and malleable you will lay it around the blow tube. You will build this up and it will look like what a potter does with clay when they make a pot. Hence the name coil pot. Once you have this built up you can melt it all together into a bubble and then you can make a tube or what ever you want with it.
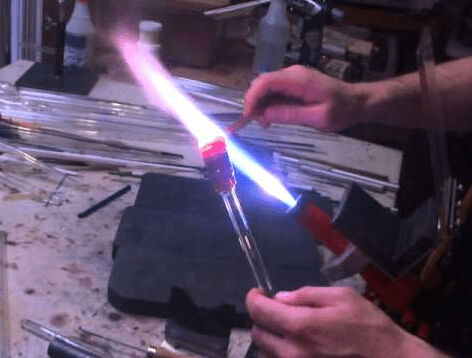
Back to Top
Color Bar-
Mostly only in soft glass color comes in the form of bar. The major manufacturers of soft glass color bar are Reichenbach, Kugler, Zimmerman and Gaffer. The process of making these involves adding metal oxides and other toxic ingredients to crucibles of molten glass, and then pulling the glass out and rolling it
into bars.
Back to Top
Compatibility-
Different glasses that have the same COE are said to be compatible. This means that they can be joined together while hot without breaking apart when cool.
Back to Top
Copa Traditional and Triangular-
Often a source of more question than answers will make an ordinary wrap into a perfect half-round. The diameter and perfection will vary with the size of the wrap and the person using the tool. The triangular copa will make crisp triangular wraps that will vary in size with the amount of glass applied. Augustine Fresnel found that triangular wraps (prisms) have great optical properties.
Back to Top
Cracking Off-
The technique of breaking off the punti or rod that has been used as a handle during the forming process.
Back to Top
Crimps -
Used in glass to smash or mash the glass. It leaves a pattern in the glass as you press it. Used to texture leaves or make any kind of pattern really.
Back to Top
Cuts and Burns-
These can be avoided with common sense and care. The most common minor burns occur when someone picks up the end of a glass rod or tube, forgetting that it is hot. A simple system, such as always laying the hot end of a rod away from you, can help you remember which end to grab. Arrange your work area so that you never have to reach in front of your torch to get a tool or piece of glass. Choose your work clothes carefully, avoiding synthetic fibers, long loose sleeves, and shirts with open pockets or pants with folded cuffs. Burns can be treated with ice, aloe vera sap, cold cider vinegar, or a variety of home remedies. Treat your injuries with respect; serious cuts or burns may require professional medical attention.
Back to Top
Devitrification-
It is the crystallization in a formerly crystal-free (amorphous) glass Devit by a blower - This is that old man look, the part of the glass that does not shine. It is like small tiny wrinkles, or it can be whitish. There is a lot that causes this. Sometimes in boro, it can be fire polished out, sometimes it's over and you have to sandblast the glass. (Ever wonder why that piece was actually sandblasted? Well this could be the reason why). Anyways this usually happens on a piece of glass that has been overworked or has gotten lots of stress. Now sometimes we call a spot devit, even when it is not. Rather it is a spot that has lots of stress from a bend or something and should have been fire polished. Either way not what we are looking for in the glass game. If it is true devit, well then it's stuck there and cannot be fire polished off. One neat technique that sometimes can help solve this is basic table salt. I do not know if you burn too much sodium out of the glass, but if you pour some salt in the flame and let the burn of the salt hit the glass, it can make the devit go away. Just try to avoid it altogether.
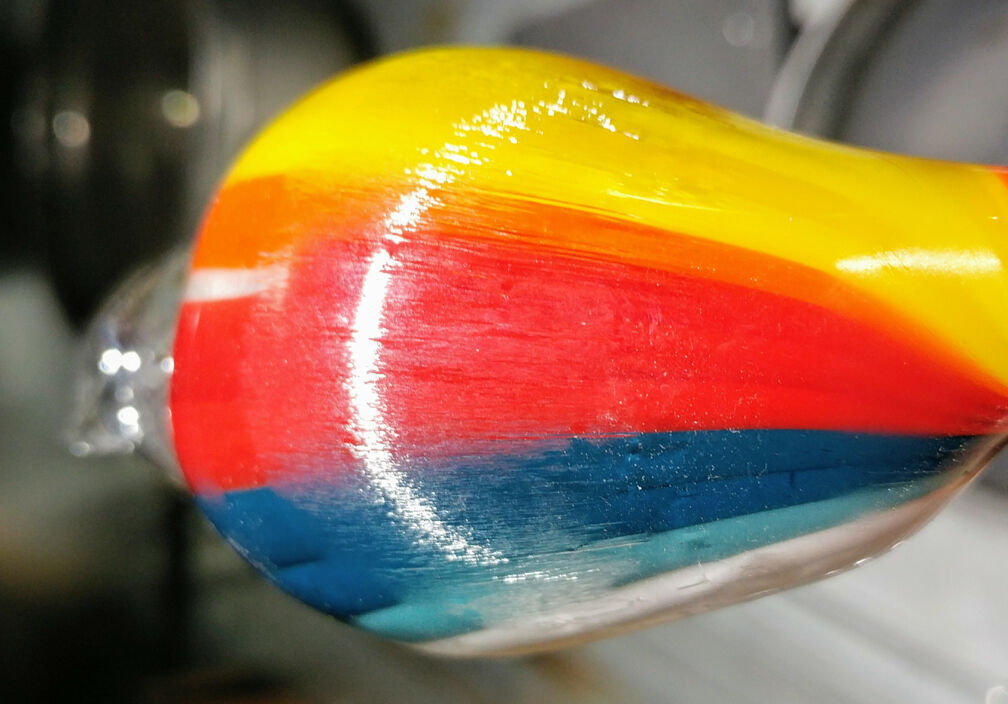
Back to Top
Diamond Shears -
Special pliers with a sharp diamond shaped opening for cutting glass and, typically, a round opening at the tip for controlling punties, pulling glass, etc.
Back to Top
Dichroic Glass-
Basically glass which has a thin metal coating applied to give it a reflective tint. Dichro by a blower - So thanks to NASA we have this really neat glass to play with that is all sparkly. What they do is some how they vaporize these metals in a vacuum and they then adhere to the glass sometimes only 1 to a few molecules thick. Different kinds of metals give us different colors with nearly 45 as of now. Okay, so now we have this glass with metal on it right, but we have to not burn it off and get it trapped between glass. What the blower must do is cover or back the glass with clear or a color. Backing the metal with a color adds yet another dimension to the glass! Once the blower makes that glass, he/she then takes it and lays it inside another piece of glass. Now there are a million ways to do this, but this is one of the most common today.
5 tips for working Dichroic Tubing 1. Always warm the tubing in the kiln at 1050°F for at least 20 min before use. The dark cobalt can get a rose color strike if it sits above 1050°F for too long. But this does not affect the stability of the glass. 2. When entering the tube into the flame use a large high oxygen bushy flame. This is a thick piece of glass so don’t short yourself on heat. A small pointy flame will not be able to heat it up enough and will cause it to crack when entering into the flame. 3. For brightest dichroic color use a high oxygen bushy flame. The goal here is to avoid the bright white heat state. To test the flame, you can put the end of a 6 mm rod in the flame and it will gather and get bright orange but will not get bright white and drip off the handle. You want to stay in the red to bright orange level. Think core heat vs. surface heat. 4. Be careful not to blow the material out too thin. It is very difficult to get it to condense back down once blown out. The encasement is very thick so when you either stretch the tube down or blow the tube out, the outer clear layer does most of the expanding leaving the dichroic layer very dense and un-stretched. 5. To achieve bright clean terminations use a carbon paddle in the flame to push the point in rather than melting it in. Heat the thicker base of the termination as you press in, rather than the tip.
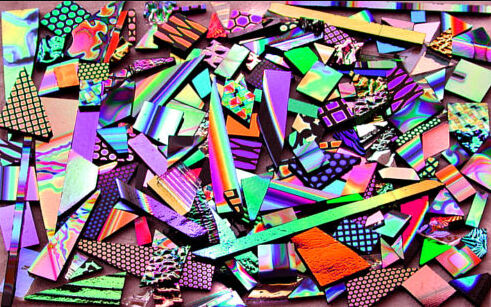
Back to Top
Didymium Glasses -
These are the basic safety glasses of the glass industry. They mostly filter the sodium flare and UV rays. These are really only good for soft glass and boro and quartz require a filter that will also filter the IR.
Words of wisdom - Go and get the good ones. Get the darkest you can work in. The more you can filter the better it is for you.
Back to Top
Digital Controller (Digitry)-
The Digitry is the standard annealer and/or furnace controller used in modern glass studios. It controls up to five separate annealers and is extremely easy to program and control.
Back to Top
Double Disappearing Weld (Jesus Seal)-
This is a special technique commonly used with making complex water filters such as a Kleincycler and Recycler. This is where a tube is joined to the main body of the glass piece, by carefully glassblowing a bubble in between the two pieces.
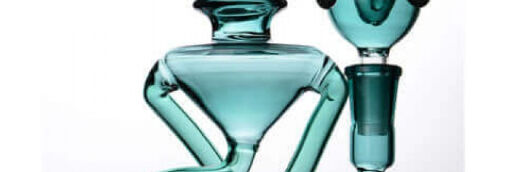
A blowers point of view - This weld is extremely difficult if you do not know what you are doing. Once you know you know. The trick is to get one part of the tube welded so that you can blow into the tube and the body of the piece you are working on. You want the tube to finish about 5-10mm from the body. Then with the torch heat up the tube and body so when you blow you can blow two bubble that will touch each other. When you do this you want them to touch and touch to make about a 5-7mm say weld. Then you come in and heat up the weld and blow out lightly. As glass wants to thicken up it will gather and pull from the inside make the two bubbles that touched a hole. Now you did it! About 55 sec. in is where the middle gives away and a hole is made.
Back to Top
Drawing-
The technique of pulling a piece of hot glass to make it narrower. We also do the normal drawing if we are making something big so we can better conceptualize it.
Back to Top
Drill Press (Core Drill)-
This is a drill that is made to be more accurate than a hand-held drill. For more info on a press see the Drill Press link
Back to Top
Dust Mask (Respirator) -
These tools are very important when working with any kind of dust. If it is a light dust you can get away with a dust mask. But if you want to be really safe, spend the extra money and get yourself a respirator. It will last a long time and is a better filter. Be safe, it's your health and you're going to live longer than you think.
Back to Top
Electroforming-
Our basic definition of this is a metal forming process that allows metal to form on something. The process is done in very clean water. There is a piece of metal and some current that is put into this water solution. When there is current the electrons move from one thing to the other.
Back to Top
Etching Cream -
Etch All is the re-usable liquid glass and mirror etch. Chemically etch your glass beads to produce a soft velvet matte or satin finish and look. Your finished product will be fingerprint proof and able to retain oil or acrylic paints and inks. Complete instructions are provided on the bottle for a quick 15 minute etch! Works great on all glass, mirror, ceramic, porcelain, marble, or slate products. Does not work so good on borosilicate glass
Back to Top
Exact Torch -
The Exact torch is the standard high-pressure torch used in glassblowing to heat specific parts of a work-in-progress. It is a modular system with interchangeable heads that go up to about 400,000 BTUs.
Back to Top
Eye Protection-
Eye protection is very important in lampworking, for two reasons. First, glass can sometimes shatter when placed directly in the flame, and you must protect your eyes from flying glass fragments. Goggles or glasses with side shields are good for this. You must also protect your eyes from potentially damaging Ultraviolet and Infrared rays, which are emitted when you melt glass in a flame. For many years, the standard eye protection for lampworkers has been “didymium” glasses, which have the additional feature of filtering out the distracting yellow glare given off by molten glass. In recent years other types of protective eyewear have become available, some of which are superior to traditional didymium glasses. The type of protective eyewear that is right for you depends on the type of glasswork you will be doing. For instance, making beads would give off less radiation than working a large piece of borosilicate tubing, which in turn gives off less than melting fused quartz. Also, different people may have different sensitivity. Please protect your eyes. Check with your optometrist and other reliable sources for more information on choosing eye protection.
Back to Top
File -
A device used to scrape off metal and can also be used to notch glass. Its a great handy tool to get you some silver shavings so you can do some universe marbles. These small shavings help give you that comment effect.
Back to Top
Filigrana
A rod of glass that has color in the middle and clear around the outside
Filigran by a blower - What a neat technique! There are a few ways to make this. First you can take a clear tube that is just larger than the color rod. Put the color rod into the tube and get all the air out. You now have a filigrana. You can also accomplish this by coating the colored rod with clear glass.
Back to Top
Fin Mold -
If you're ready to take on the tricky world of faceted goblets you might consider a Fin Mold. Once you learn to master it, your patience will be rewarded with crisp facets. Fin Molds come in four different profiles with stainless steel construction.
Back to Top
Fire Polish
Simply when you take fire and polish an end of the glass. This is used to make the end of the glass shiny if it was cut or cracked off. It also makes the glass smooth so it will not cut you. The tube on the right has been fire polished, while the tube on the end was scored and cracked leaving a sharp end that could CUT you. These are plain dangerous in the shop. They are really really dangerous if they are a blow tube. Fire cut or fire polish your ends.
Back to Top
Flare Tool -
A flashback arrestor or flash arrestor is a special gas safety device most commonly used in oxy-fuel welding and cutting to stop the flame or reverse flow of gas back up into the equipment or supply line and it prevents the user and equipment from damage or explosions.
Back to Top
Flame-Annealing
A flameworking technique where the finished piece is reheated in a bushy, relatively cool flame to relax the stresses built up in it during the construction process. This is usually used only on small pieces and is generally regarded as a temporary measure for work that is to be properly annealed later on.
Back to Top
Flame-Cutting
Any technique where the flame is used to burn apart two pieces of rod or tubing. You cut the glass with a flame baby!
Back to Top
Flameworking
Also known as lampworking or lamp-blowing. The technique of heating, melting and forming glass rods and tubes using a flame generated by a burner or torch.
Back to Top
Flaring
This when a blower takes a tube and heats the end up. Then they use a tool or G'forces to open the end of the tube.
Back to Top
Flashback Arrestor -
A flashback arrestor or flash arrestor is a special gas safety device most commonly used in oxy-fuel welding and cutting to stop the flame or reverse flow of gas back up into the equipment or supply line and it prevents the user and equipment from damage or explosions.
Back to Top
Fluorescent Light Transitional Glass-
This is glass that changes color when it is under fluorescent light. The minerals that go into this are TOP SECRET. There are a lot of new colors coming out that change this way. We are not sure why they call it CFL glass as CFL stands for (compact fluorescent light), but ya this is the industry terms.
Back to Top
Foot Pedal -
A device used to usually turn the outer flame off on a larger bench torch. This is one of the best upgrades a blower can do for themselves. Two of the top brands we have seen over the years are the super reliable set from Griffin Glass. The other is also great from Jeff Rogers.
Back to Top
Fork (Pastorale Fork) -
The fork is a long metal rod with a forked end on it, used to load work into either a garage or annealer. The fork is typically used when making goblets and other Venetian-style work.
Back to Top
Founding-
Heating the glass to a proper usable temperature.
Back to Top
Frit
The glass that is broke down very small so that looks like sand. This can be from near powder to large 8mm chunks. Most commonly used is small to large that is about 1-4mm.
Back to Top
Frit Maker (Crusher) -
This is a device you can use to smash glass into small pieces called frit. Basically a tube with a bottom that can hold the glass. Then another tube with a metal part to smash and a handle on it. Put the glass in, lift the handle up and let is smash the glass, now you have frit you will have to sift.
Back to Top
Frit Tray -
A device used to hold frit while a blower rolls hot glass in it.
Back to Top
Fuming
This glass technique is one of the first basic techniques learned by a blower. It is very simple and silver is inexpensive for what it does. Gold is a little more costly, but it takes fuming to the next level.
Silver Fuming
The glass must be hot in order for the silver to stick to it. Preheat you piece of glass using nearly any size tube or rod, you can even fume colored glass. First, you must also have a rod of glass with a piece of silver on it. To do this you heat up the glass 5-10mm rod with a small small piece of silver cut and laying on your graphite. I prefer about a 6mm piece of clear glass. If your silver does not stick the first time heat the glass up again and press on the silver until the silver sticks to the glass. Once you have this not back to that piece of glass you want to fume, again make sure it is hot. How I prefer to fume is turn my torch down to a small neutral almost reduction flame. Then I put the silver in there and it will start to smoke, but sometimes is splattered first, I do not like this unless I am using it for a special technique. So I let it splatter than once it does that I then put my glass I want to fume into the flame and spin it. Now you can do too much here, only cover it. If you do too much you can burn it off with an oxidizing flame. Fuming is all about the application. Ones you have your glass fumed with silver you can do all sorts of things with it.
Gold Fuming - Gold takes fuming to the next level. Gold is best fumed on top of silver, I prefer just a slight silver fume under the gold. This also is what gets some super dope greens, what I just love! To get the gold to fume you need a little hotter more oxidizing flame. I use the same little flame for silver, just turn up the oxygen a little and it will get the gold hot enough to fume. Once you have the glass fumed you can sleeve it, draw clear lines or dot it up. You can also fume the outside or inside of the glass. Both give amazing and unique effects. Did you know at a microscopic level gold is red. The first nanotechnology was done by glass artists many, many moons ago.
Back to Top
Fused Quartz-
Glass consisting of silica in amorphous (non-crystalline) form. It differs from traditional glasses in containing no other ingredients, which are typically added to glass to lower the melt temperature. Although the terms quartz and fused silica are used interchangeably, the fundamental structures and creation of each glass differ. Fused silica, therefore, has high working and melting temperatures. The optical and thermal properties of fused quartz are superior to those of other types of glass due to its purity. For these reasons, it finds use in situations such as semiconductor fabrication and laboratory equipment. It transmits ultraviolet better than other glasses, so is used to make lenses and optics for the ultraviolet spectrum. Its low coefficient of thermal expansion also makes it a useful material for precision mirror substrates. Quartz by a blower - This is typically what your bangers are made of. Really any glass you will heat up over and over and cool down rapidly by putting oils on the glass. See how to tell if your glass is really quartz
Quartz :
COE of 5.5 ⋅ 10−7/K (average from 20...320 °C)
Softening point: 3029 F, 1665 C
Annealing point 2084 F, 1140 C
Back to Top
Garage-
An oven or kiln used when making complicated work made from many parts. The parts are kept warm in the garage or kiln until needed. For example, when making complicated rigs, goblets, or just big things, parts are made and then stored in the garage. For a goblet, the foot is made, and then the stem is brought from the garage and attached. Finally, the bowl is brought and attached to the top of the goblet. For soft glass the right side (cold side) of the garage is kept around annealing temperature (900 F), the left side is usually around 1050 F. For borosilicate the garage temperature can be set at 980 for less intricate pieces and 1080 for more complicated pieces.
Back to Top
Gather-
Any mass of molten glass collected on the end of a punti or rod. This is usually accomplished by holding the hot part of the rod up and letting it fall back onto itself.
Back to Top
Glass Forums-
This is where blowers will go for information from other blowers. Here are a few we have found and like. Lampwork Etc.
Back to Top
Glass Gong -
This is used on rare occasions when something very very special happens. It may only be rung 20 times a year. The higher your skill set, the harder it is to obtain a GONG.
Back to Top
Glass Rod Warmer -
This tool is used to pre-heat your glass rods. This allows you to get them molten much faster, while also saving fuel and oxygen.
Back to Top
Glass Storage-
This is a place or thing you store your glass in.
Back to Top
Glory Hole -
These furnaces are mostly gas-fired and are used to reheat work that in in progress. They can range in many sizes from commercial use to home use. The doors on the front can be moved to accommodate larger glass going in and out of he glory hole. Used mostly in soft glass, but sometimes in boro glass. Marcel is the guy in the borosilicate world breaking the rules with these things.
Do not get this glory hole confused with those other glory holes found in bathrooms. Just not the same, stay away from the bathroom glory hole, you may get some fire there, but its not good fire.
Back to Top
Graphite -
Basically carbon, it is the most stable form of carbon under standard conditions.
Graphite by a Glassblower - This will be found in any blowers arsenal. U,sually it will be in flat plates that a blower will roll their glass on, or it will be in the form of a rod. The graphite can withstand shit tons of heat and can also be put in water without damage. Its easy to grind or carve for a simple mold.
Back to Top
Ground Glass Forming Tool -
This is used to make those ground glass joints. Basically, it is a tool that has a mold on the inside and two parts on the outside to mold the glass. As you heat up the tube you insert the tool into the hot glass tube and then press the outside to get the shape of the tool. Here is an example of an Elev8 Premier tool we make our joints on.
Back to Top
Ground Glass Joints
These are what you see on all the glass water pipes and rigs. They have been around for a very long time. Many of the joints that come from Germany are made on a machine. Many of the joints that come from China are made by hand. Both are great, just one puts more people to work. The USA has also started making joints in clear, while many of the top artists make their own joints.
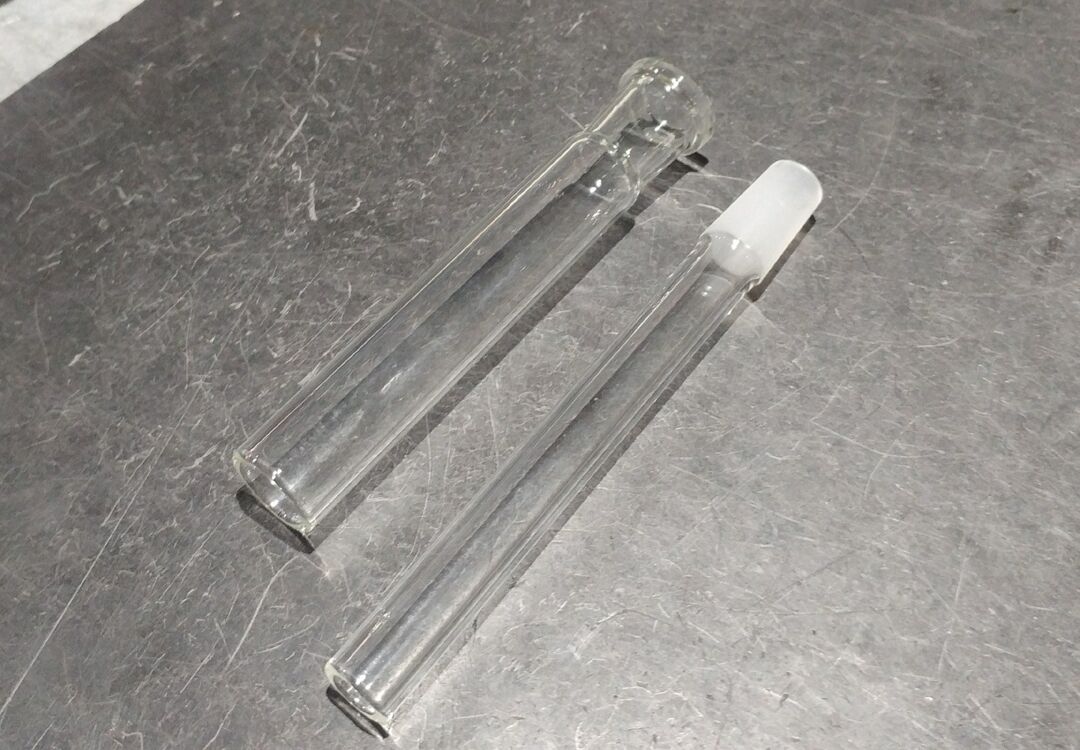
Back to Top
Gun Case For Pipes-
A plastic case that has foam inside to protect the contents. They work perfectly for glass.
Gun Case by a Glassblower - This is used to take all your glass to the sell it. As a glassblower, you will need to learn to sell what you make. People only by from people that are selling. This is a very inexpensive tool that if you treat it right will last a long long time.
Back to Top
Hammer Pipe-
A hammer pipe gets its name from its shape. It looks like a hammer. You can see more hammer pipes here.
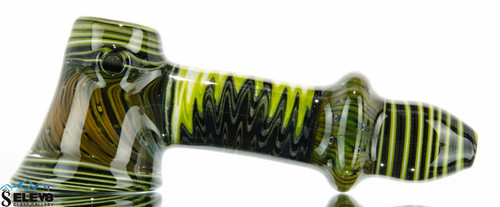
Back to Top
Hard Glass-
A common name for borosilicate glass. It has a COE of approximately 33.
Back to Top
Hazards-
These can include muscle strains or other injuries from maneuvering heavy oxygen tanks or repetitive movements (such as making hundreds of beads). Take frequent breaks and pay attention to your body’s signals to minimize these types of injuries. Check for an accurate height of table to chair for comfortable work. Dehydration and heat exhaustion are other possible hazards to watch out for. Drink plenty of water, especially if you are working with a large flame. You may also consider applying sunscreen to your skin to protect it from the radiation given off by the flame. The following references may be useful in protecting yourself from the common hazards of lampworking: Artist Beware, by Michael McCann, available from Center for Safety in the Arts, 5 Beekerman St., Ste. 280, New York, NY 10038 Contemporary Lampworking, A Practical Guide to Shaping Glass In the Flame by Bandhu Scott Dunham, available from Salusa Glassworks, P.O. Box 2354, Prescott, AZ 86302 Glassblowing: An Introduction to Solid and Blown Glass Sculpturing by Homer L. Hoyt, Crafts & Arts Publishing Co. Inc, 626 Moss St., Golden, CO 80401 The Artist’s Complete Health and Safety Guide by Monona Rossol, available from Allworth Press Ventilation–A Practical Guide for Artists, Craftspeople and Others in the Arts by Nancy Clark, Thomas Cutter and Jean Ann McGrane, available from Center for Safety in the Arts “Beads from the Beginning” by Brian Kerkvliet, Glass Art Magazine, November/December 1994, P.O. Box 260377, Highlands Ranch, CO 80126 “F.Y. Eyes” by Lisa M. Malchow, Fusion Journal of the American Scientific Glassblowers Society, May 1993. 1507 Hagley Rd., Toledo, OH 43612 “Glassmaking Health and Safety” by Monona Rossol, Glass Art Society Technical Journal, 1989. Reprint available from Allworth Press “Optical Radiation Hazards in Glassblowing” by Gary E. Myers, Fusion Journal of the American Scientific Glassblowers Society, August 1976
Back to Top
Heady Glass-
Heady Glass is a style of glass that is incredibly artistic. By incorporating lots of colors, as well as advanced glassblowing techniques, glass made in the style is very much one-of-a-kind! Many glassblowers, such as those in our Elev8 Glass Studio, specialize in particular techniques and do custom work to make a name for themselves.
Back to Top
Health and Safety-
Like any craft or hobby, glass working has some inherent risk of injury to the artist. As interest in lampworking has increased, it has become clear that general information on potential health and safety risks would be useful. The following information is intended to increase your enjoyment of lampworking, while adding to your awareness and helping you reduce your exposure to potential hazards. These suggestions have been prepared and reviewed by a group of experienced lampworkers. This is not intended to be a complete list of all hazards associated with lampworking, other hazards may exist.
Back to Top
Heat Protection -
You need this when you go big. There are a lot of different kinds of protection from sleeves, leather vests, full metal jackets. The harder you go, the bigger the flame, the larger the radiant heat, the more protection you need.
Back to Top
Hose -
This is what a blower or welder uses to hook up their oxygen tanks to their torches. The red is used for fuel and the green is for oxygen. There are different grades of these hoses, so make sure you know what you are looking for and talk with your welding supply store. We know grade T will work for propane.
Back to Top
Hose Clamp -
This is used to secure your hoses to your connections. Any time you make a connection you should spray it with soap to make sure you are 100% good to go.
Back to Top
Hot Fingers -
These are also called claw grabbers or holding clamps. See also holder or claw fingers for more styles.
Back to Top
Hot Plate -
Electric and gas hot plates have many uses in a hot shop. They are used most frequently to preheat bits of color or murrini so that the color does not crack upon contact with the work-in-progress.
Back to Top
Implosion (Bubble) Tool -
In the flower industry, they call this a frog. Ya, a strange funny name for such a tool. Basically, a tool that has a bunch of pin in a pattern.
Implosion Tool by a glassblower - This tool is used to get all those neat bubble implosion style marbles. Simple gather some hot glass and then push it down on this tool. It will put a bunch of indents in the glass. You then take some color or fume it and then add clear to all the pushed indents and you trapped some bubbles in the glass.
Back to Top
Incalmo-
Incalmo is the advanced technique of joining two glass bubbles of different color together. Typically, one bubble is opened into a cup shape, and then attached to a punty, and the other is opened into a cylinder on the end of the pipe. The cup is then joined on the cylinder to make a two-color piece.
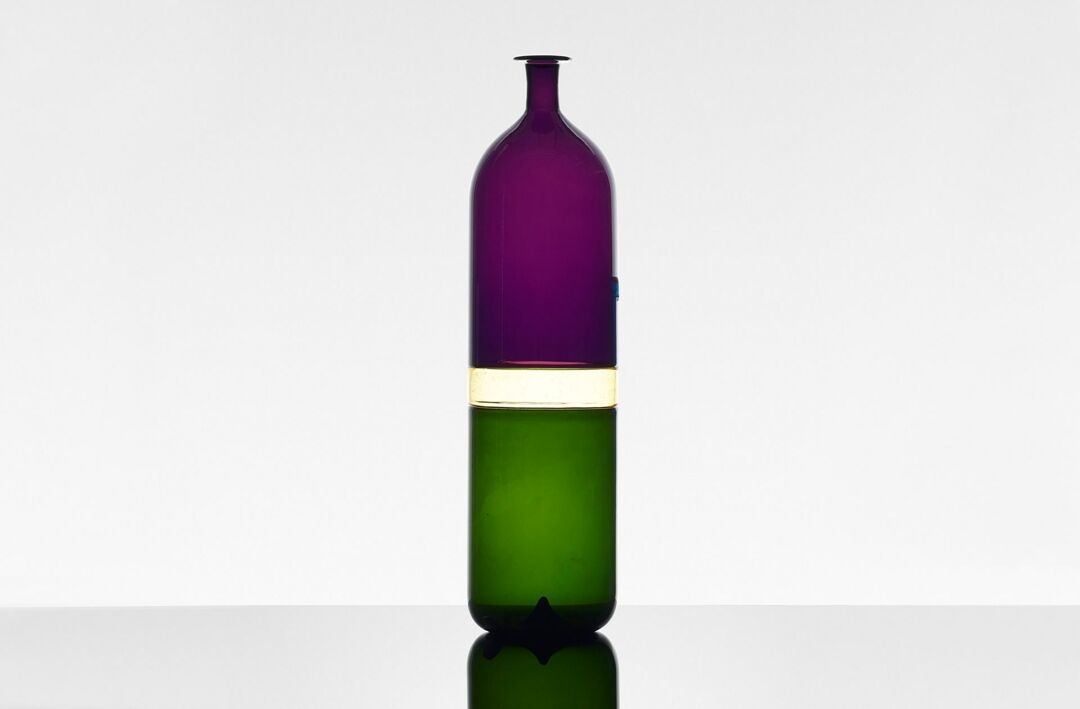
Back to Top
Infrared Heater -
A device used to heat up the studio. Because the air flow is so great standard heaters will not work as they heat the air and it will go right out the exhaust. Elev8 Premier has invested in these to keep the super cold winter days workable.
Back to Top
Inside Out Work-
This is glass that has a layer of clear on top of it. This can be accomplished with a few techniques such as puff and stuff, flipping, or just opening a tube and drawing inside. It can also be as easy as dumping frit inside a tube and melting it in.
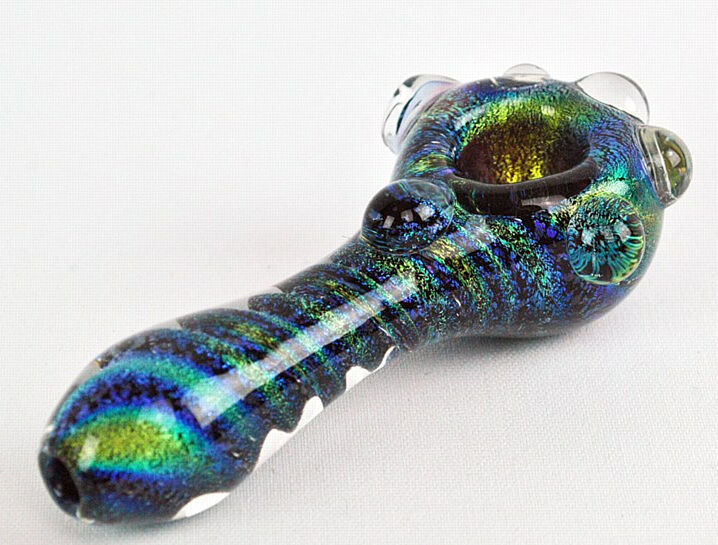
Back to Top.
Iridizing or Iridized Glass-
A technique involving spraying hot glass with metallic salts to give and iridescent finish. Requires very good ventilation.
Back to Top
Jack's Tool -
A hairpin-shaped tool with long blades for shaping glass.
Back to Top
Kevlar (Sleeves, Gloves, Pads) -
This has many applications, ranging from bicycle tires and racing sails to bulletproof vests, because of its high tensile strength-to-weight ratio; by this measure, it is 5 times stronger than steel. It is also used to make modern drumheads that withstand high impact. When used as a woven material, it is suitable for mooring lines and other underwater applications. In glassblowing, we use it because it also has a high-temperature rating. We use it for sleeve, gloves, and pads.
Back to Top
Kiln Posts -
These are used to hold up a kiln shelf, keep a tube held up, or we even use it to keep the kiln door better closed during the annealing process.
Back to Top
Kiln Wash -
A kiln wash is a sacrificial layer of material between your glass and your kiln shelves. It's primary purpose is to prevent glaze from sticking to your shelves. The ingredients are materials with high melting points, with the formula adjusted based on what temperature you are firing to.
Back to Top
Klein Bottle-
An example of a non-orientable surface; it is a two-dimensional manifold against which a system for determining a normal vector cannot be consistently defined. Informally, it is a one-sided surface which, if traveled upon, could be followed back to the point of origin while flipping the traveler upside down. Other related non-orientable objects include the Möbius strip and the real projective plane. Whereas a Möbius strip is a surface with boundary, a Klein bottle has no boundary (for comparison, a sphere is an orientable surface with no boundary).
The Klein bottle was first described in 1882 by the German mathematician Felix Klein. It may have been originally named the Kleinsche Fläche ("Klein surface") and then misinterpreted as Kleinsche Flasche ("Klein bottle"), which ultimately may have led to the adoption of this term in the German language as well.
Back to Top
Knock Off Table -
The knock off table is an essential piece of hot shop equipment for making production-line work. It is covered with a woven silica fabric that can stand the heat of a freshly made piece and will not wick enough heat from the piece to cause a check. A piece can be knocked off onto the table, and then a torch can be used on the punty spot to soften any sharp edges before the piece is placed into the annealer.
Back to Top
Lab Coat -
At Elev8 Premier, we use the lab coat when we are working in the wet room. We use this for when we are grinding or cutting glass on the lapping wheel or on the wet saw. Glass dust gets trapped in the water, this is good! The issue that can arise is that when the water dries you have a bunch of glass dust on your clothes. We use this to catch that water dust and then wash it after each use. Always wear a dust mask while grinding or cutting also.
Back to Top
Lampworking
A type of glasswork where a torch or lamp is primarily used to melt the glass. This is the standard way of making glass in the borosilicate art world. Once in a molten state, the glass is formed by blowing and shaping with tools and hand movements with gravity being one of the most useful tools. Although lack of a precise definition for lampworking makes it difficult to determine when this technique was first developed, the earliest verifiable lampworked glass is probably a collection of beads thought to date to the fifth century BC. [1] Lampworking became widely practiced in Murano, Italy in the 14th century. In the mid 19th century lampwork technique was extended to the production of paperweights, primarily in France, where it became a popular art form, still collected today. Lampworking differs from glassblowing in that glassblowing uses a furnace as the primary heat source, although torches are also used. The term lampworkig and glassblowing are very intertwined these days.
Lampworking is used to create artwork, including beads, figurines, marbles, small vessels, Christmas tree ornaments, and much more. It is also used to create scientific instruments as well as glass models of animal and botanical subjects.
Back to Top
Lapping Wheel -
This is a tool used to make glass flat. Many times it is used to facet glass into beautiful shapes like a diamond, or to make a piece of glass sit flatter. A lapping wheel is made from a rotating wheel covered with an abrasive, usually diamonds. When grinding on a wheel you will want water to always run on it as a lubricant and to keep the glass dust down. Always wear a dust mask.
Back to Top
Lathe for Glass -
This is a machine that spins the glass for the blower. A glass lathe is unique in that it spins the chucks on both sides of the lathe, while wood and metal lathes only spin on chuck. As the glass gets soft it needs to spin as the same speed on both sides. So with both sides of the lathe spinning it allows you to work a glass tube or rod uniformly.
Back to Top
Lazy Susan for Glass Blowers -
This is an amazing tool if you can swing it. We made our own here at Elev8 Premier as who does not need more space?? Put your frit in it, small tools, sunscreen or I bet you can think of all kinds of things.
Back to Top
Lighter (Zippo, Striker) -
This is the tool used to start the fire on your torch. NEVER USE A BIC OR ANY KIND OF BUTANE LIGHTER. These can explode when they get hot. Get some style and get a dope ass zippo. If you find a zippo you like, Elev8 Glass Gallery can even get it engraved for you.
Back to Top
Line Work-
Line work can mean a lot of different things. We believe line work is a tube of glass that is colored with rods of glass. This line work tubing is usually made into switch balls and then put back together. It is made by a number of techniques. These techniques include but are not limited to:
- Flaring open and drawing the lines in with stringers:
- This is done by opening up a tube of glass and flaring it open. Then pull stringers about 2mm thick. You will then draw lines down the flared tube. You will notice the open end is a larger diamter from the side welded to the blow tube. This will cause you to make a "V" patern as you color the glass. This is ok and you will not even see it. Melt it down and you have some line work tubing. This also makes great tube work for terminations as you have just clear glass over color.
- Stick Stack:
- This techniques is when you place rods of color inside a tube of clear glass. The way we do it at Elev8 Premier is that we take a 50mm tube and a 1 inch graphite rod. We cut the color down to size and lay it around the graphite. Put a rubber band around the glass and graphite. Then you will insert this into the clear glass. Once inserted you will remove the rubber band and start to melt it down. Once you get some of the color to stick to the clear you are good. You can remove the graphite and work it all down into 1 piece of glass. You know have a line work tube of glass. We prefer this method as one of our favorites as you tube is clear over color and you can get some great terminations.
- Vac Stack:
- Yep and this is kinda what the big boys do to go fast, have a lot of color and get some weight. So how we do it here at Elev8 Premier is we use a 80mm x 9mm clear tube of glass. Then we put 26 rods of color around a 45mm heavy wall tube of clear. We put the 45mm inside the 80mm tube, then we lay the rods in between these. Once all the color is in there we begin to melt it. Pull and you now have line work tubing. This is great to work with, nice and thick and just has a lot of lines of color. One thing you have to have good skill is on your terminations. This makes great line work, but the tube (looking at the open end) out is clear, then color then the inside is clear. What this can cause is when you terminate that clear will pull through and make like a fish eye. You need to have your termination skill set on point before you attempt terminations on this kind of line work tubing.
Back to Top
Local Exhaust Ventilation -
One of the most important tools to the blower. This needs to be strong enough to move the air and make sure that if you are doing any fuming all the extra fume is removed from your surroundings. The rule of thumb is that it will be able to pull up some toilet paper from your hand into the exhaust. Go bigger than smaller.
Back to Top
Mandrel -
A round object against which material can be forged or shaped. Usually made of graphite in this industry. Below is an example to of a ring mandrel.
Back to Top
Mandrel Rack -
This item is used to rest mandrels on. Sometimes used next to a kiln so the beads can sit in the kiln and the handle on this rack.

Back to Top
Marble-
A round piece of glass. Usually with some kind of artistic style to it. They can be from a small 1/4 inch piece to a massive 8 inch the size of a bowling ball.
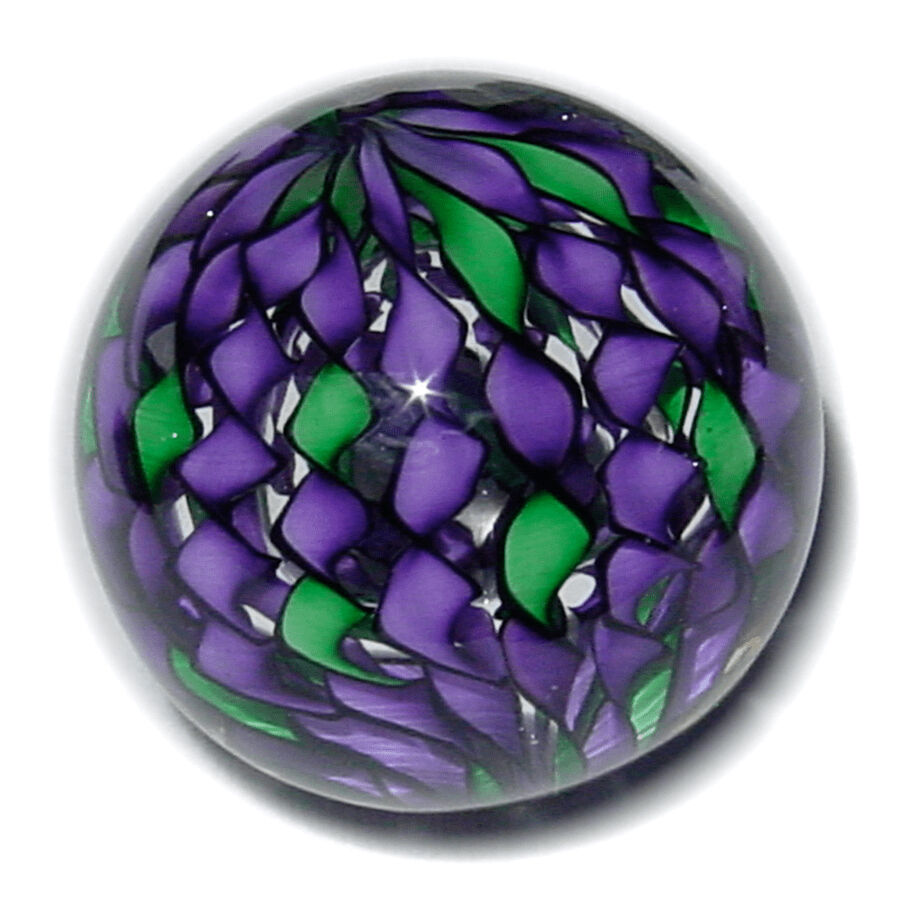
Back to Top
Marble Mold -
A marble mold us mostly always made from graphite for the ease of machining the graphite along with the high-temperature resistance it has. They come in many shapes sized and styles. Here are some of what Elev8 Glass Studio uses in house.
Back to Top
Marble Tongs -
A tool that is designed to grab a round marble where tweezers will let the marble fall. Usually, much like a pair of large tweezers but on the open end there is a ring.
Back to Top
Marbling
This is a technique that is loved by Elev8 Premier, particularly Steve. Glass does not get wet enough so that the color can move through, so the artist must lay the colors he/she wants on top of their main color. Then mix it in so it appears to be marbled, well I guess it is if it looks like it.
Back to Top
Mariah-
This is where he blower heats up a tube and pushed it together to make a ridge or narrow band. It makes a ring around the tube.
Back to Top
Marver (Paddle)
This is a process of shaping the glass with a tool. Also it is a tool used in glassblowing. It generally is made of a polished steel, brass, or graphite surface attached to a metal or wooden table.
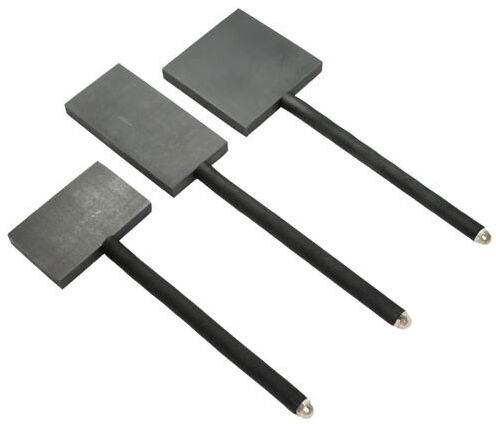
Back to Top
Masher -
masher
Used in glass to smash or mash the glass. There are many many different kinds. The most common mashers are used to mash a round ball of glass into a disc.
Back to Top
Melting Point-
The temperature below which glass acts as a solid and above which it can be shaped.
Back to Top
Metal Oxides-
When glass color is made, the metal oxides are stable and “in solution”, anytime you work with the glass, in any manner, you may be breaking open “the solution” and exposed to the metal oxides. This is a list of some of the metal oxides that may, or may not, be contained in the colored glass rods we sell, it is not intended to be a complete list: Iron Oxide, Chromium, Sulfur, Calcium, Manganese, Manganese Dioxide, Cobalt, Arsenic, Potash, Copper Oxide, Nickel, Chromium, Tin Oxide, Cadmium, Titanium, Uranium, Didymium, Selenium, Copper, Gold, & Silver.
Back to Top
Millefiori-
A combination of the Italian words "mille" (thousand) and "fiori" (flowers). Milli by a blower - Ok so all those picture chips, those are what we call millies. They started long ago with basic shapes turned to flowers. Now the technique is used to make all kinds of pictures. This is a very very time consuming technique. Lauren Stump is one of the greatest milli makers of our time. 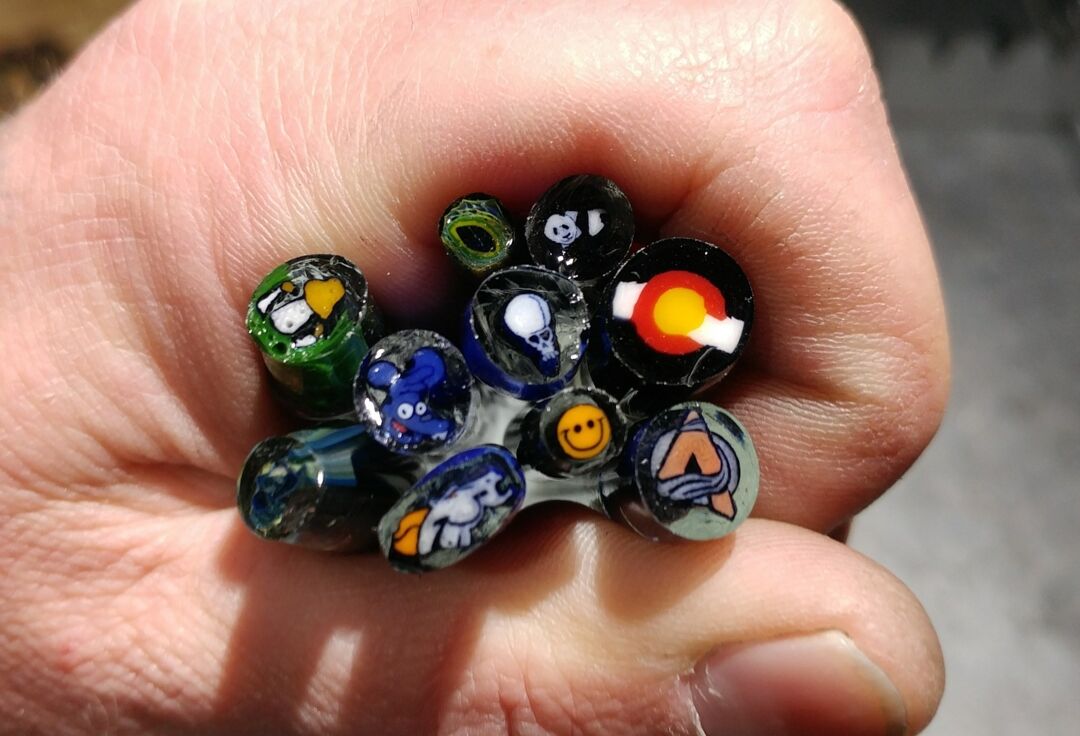
Back to Top
Mini Tube-
A mini tube is a small waterpipe usually made for dabbing. We feel a mini tube is no taller than 12 inches. After that, it becomes a standard water pipe or dab rig. Here is a list of mini tubes. Smaller than 6 inches we feel it becomes a nanotube.
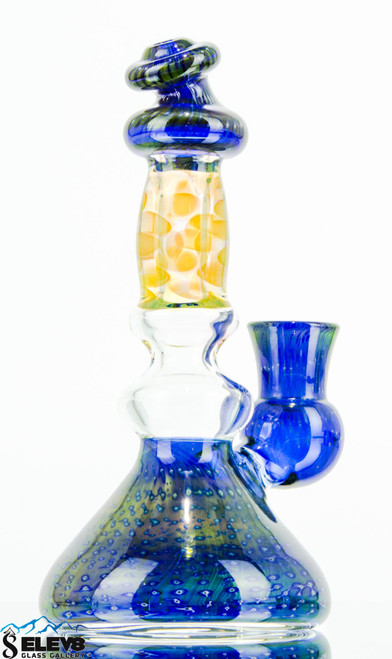
Back to Top
Mold (Mould) -
A hollow container used to give shape to molten glass or other liquids as it cools and hardens. Many times soft glass is blown into a mold, below is a bottle mold.
Back to Top
Murrine-
Colored patterns or images made in a glass cane that are revealed when the cane is cut into thin cross-sections. Murrine can be made in infinite designs from simple circular or square patterns to complex detailed designs to even portraits of people. One familiar style is the flower or star shape which, when used together in large numbers from a number of different canes is called millefiori.
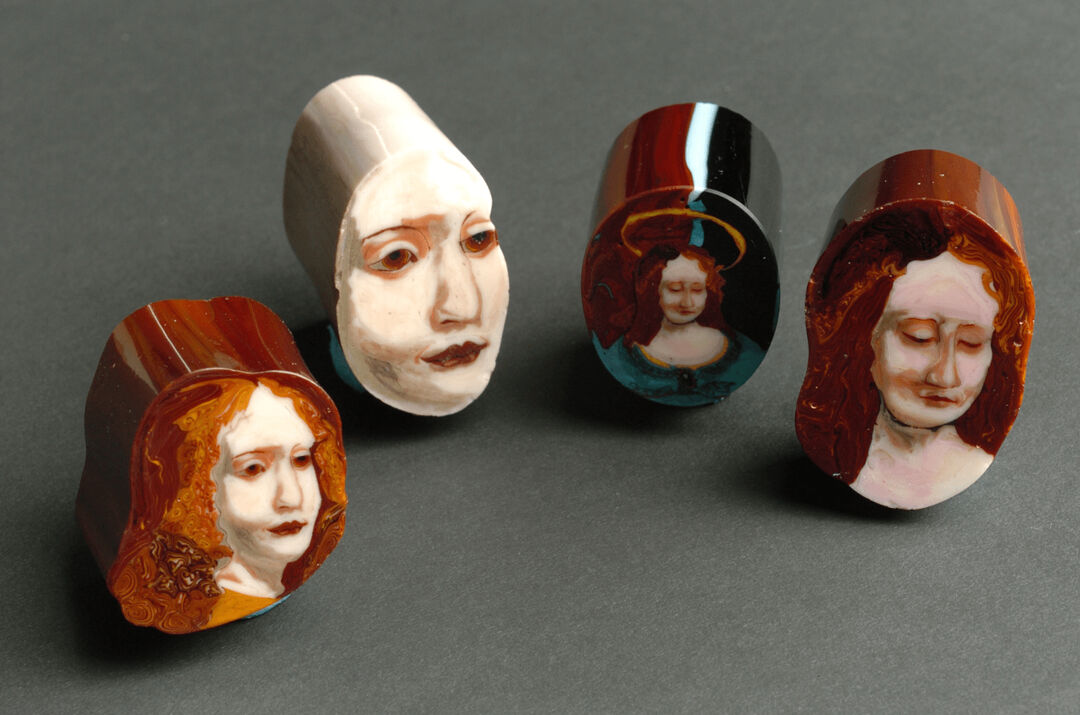
Back to Top
Necking Tool -
These tools are super great for creating very tight shaping and restrictions in blown or solid glass.
Back to Top
Neutral Flame-
This is the hottest flame on the torch. It has a good burn of the propane and not too much oxygen. How to set a neutral flame Glass Alchemy recommends you always work with a neutral flame (saving reduction for the final step)—it helps maintain consistency and vibrancy in your work and eliminates the cracking of chrome colors. The neutral flame test in borosilicate was developed at Glass Alchemy with Amazon Night, 987 and is now an industry standard. No flame will ever be neutral from base to tip and each torch has a different neutral zone. The area closest to the torch face tends to be reducing so don’t work too close. When properly set, the middle section is neutral and is the ideal flame for working colored borosilicate. Heat a rod of Amazon Night, 987 until it glows a dull orange; remove from flame and cool. If the rod does not change color, you have a neutral flame! If the rod is light sky blue1 or has a metallic sheen2 this means the flame is reducing and the propane needs to be decreased. Note: that the propane to oxygen ratio depends on the torch you are using. If the rod is sky blue, the flame is very reducing and should be adjusted by decreasing the propane pressure at the regulator (ex: from 4 to 2 pound). If the rod has a metallic luster, try decreasing the propane on the torch or at the regulator in ¼ pound increments until you are able to heat the rod without a color change.
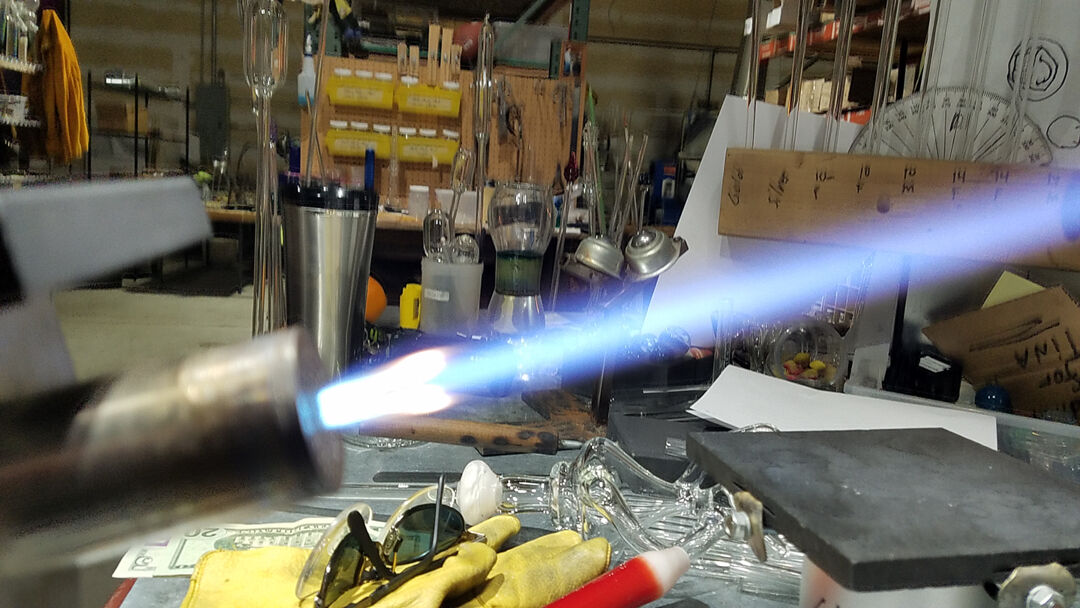
Back to Top
Nippers -
This tool is used to break off small piece of glass. Some nippers have a cutting wheel or wheels built into them for cutting glass even better. Some people use a tile nipper for this purpose.
Back to Top
Northstar Glass
This is the hottest flame on the torch. It has a good burn of the propane and not too much oxygen.
Back to Top
Nuggets -
This is the herb that a typical glass blower will consume throughout the day. Many people call this cannabis or ganja.
Back to Top
Opals-
Opal is one of the world's most beautiful and precious gemstones, predominantly found in Australia. It is one of only six types of precious gemstones found on planet earth, sharing prestigious company with diamonds, rubies, sapphires, emeralds, and pearls. You can not use a natural opal in glass. You must use a created opal called a Gilson Opal. The term, “laboratory-grown” means that our products faithfully mirror Mother Nature’s opal. Gilson-Created™ Opals have virtually identical chemical, physical and optical properties as do their naturally-occurring counterparts. The exception is that our lab-grown products are harder and more durable than most of those from nature. We no longer produce Gilson Created opal varieties in rough, uncut volumes, loose stone assortments and in fine jewelry designs. So, if technology is your fascination, beauty and affordability your pursuit...have a look. Click here to learn more about natural opals.
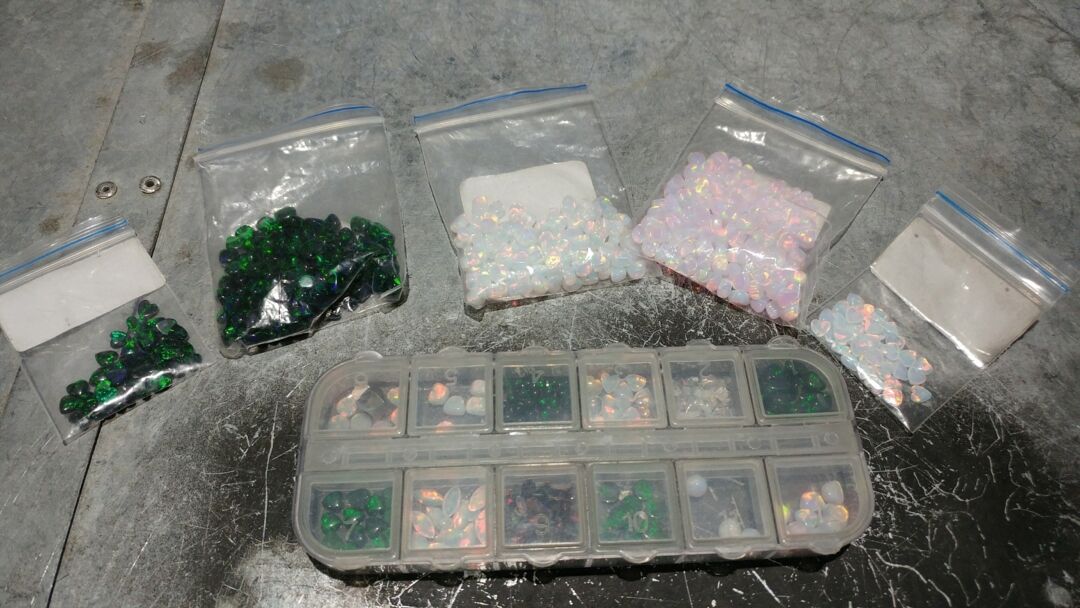
Back to Top
Optic Mold -
An open, cone-shaped mold with ridges on the inside that will impart a pattern on the surface of a gather or bubble that is inserted into it when hot.
Back to Top
Oxygen Regulator -
This device lets the oxygen run at a nice steady level so the flame works consistently. Mostly it will be used to lower the pressure and keep it steady. Many times if using a K tank or dewar tank the pressures can be 300-2000 PSI. Our GTT torches run on 12 PSI
Back to Top
Oxygen Vaporizer -
A device that is connected to an oxygen dwer when you run liquid from it. This allows the liquid to expand and give good pressure on larger setups.
Back to Top
Overlay
A thin layer of clear or colored glass is folded, formed and coated with another.
Back to Top
Oxidizing Flame-
This occurs when you run your torch with a lot more oxygen than what is needed to burn all the fuel. When you do this the atmosphere is rich in oxygen and with some glass the oxygen atom will actually bond to the glass. Running too much can cause what we call devitrification. Sometimes you do want to run an oxygen rich flame as the oxygen molecule will not adhere to some glass and you want to run it a little cooler. 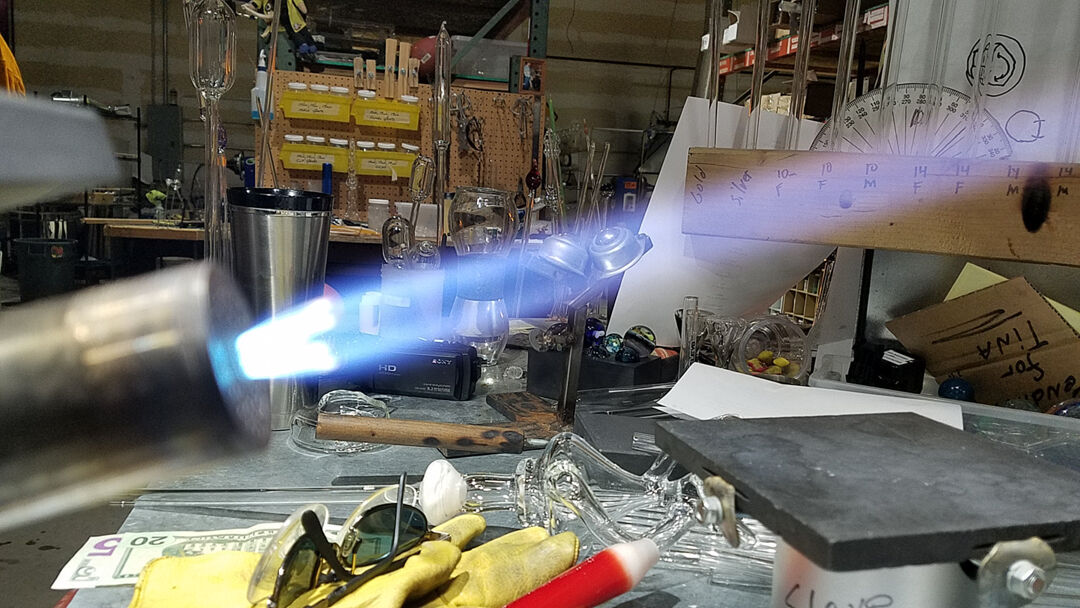
Back to Top
Parison-
The first small bubble at the end of a blowpipe.
Back to Top
Percolator-
This is the thing inside the water pipe that lets the air/smoke/vapor in small bubbles go through the water. These can range from 1 hole in a tube inside the rig/water pipe all the way to a hand sculpted piece or art that lets the air go through it. The more percs there are, the more drag there is usually as the smoke/vapor is going though more water at once and more holes. This does make the smoke/vapor cooler, but a little harder to pull. We will list all the percs we know below.
Mushroom Perc-
Because it looks like a crazy mushroom, and it will take the percolation to the next level!
Back to Top
Top Hat Perc-
Its called this because is looks like a top hat and it is a percolator.
Back to Top
Hive or Bee Hive Per-
This thing looks like a beehive and will sting you with some amazing function. Tons of slits to rip up the water!
Back to Top
UFO Perc-
Designed to take you to another world. Its in the shape of a space ship and really diffuses the smoke or vapor.
Back to Top
Sprinkler Perc-
When first made it reminded the inventor of a sprinkler head in his/her yard. Really diffused well with low drag
Back to Top
Top Hat Perc-
Its called this because is looks like a top hat and it is a percolator.
Slit Disc Perc-
A disc is made and then a bunch of slits are cut in it. Fire polished and then put inside. Offers amazing free flow percolation.
Back to Top
Jet Perc-
Shaped like the back of a jet. This thing works well, offers some drag if you are looking for that.
Back to Top
Toro Perc-
Made by Toro Glass and just looks dope, while the function is amazing!
Back to Top
Double Disc Perc -
Two discs stacked on top of each other and then cut. There is a lot of work that goes into this percolator which allows it to work very well.
Back to Top
Cross Slit Perc-
Really a lot of work goes into this percolator with the cross-section cuts and how many tubes go together to make this amazingly functioning perc.
Back to Top
Tripple Inverted Cake Stack Perc-
Percolator in percolator in yet another percolator
Back to Top
Gas Mask Perc-
Designed to gas you out of your mind with some amazing percolation. It looks like a gas mask.
Back to Top
Interceptor Perc -
Just plain amazing! The plates help break the percolation bubbles up, even more, making it an ultimate diffuser
Back to Top
Shower Head Perc-
Designed to look like a showerhead.
Back to Top
Ball Perc -
Basically they blow a ball and then cut slits in the ball. Then in the cuts the make a tack weld to help break up the air and diffuse better. These take a lot of time to make, but work gr
Beaker Perc - This is a percolator in the shape of a beaker bottom. The blower makes this shape, then he/she will cut slits in the bottom and then weld it into the water pipe or rig.
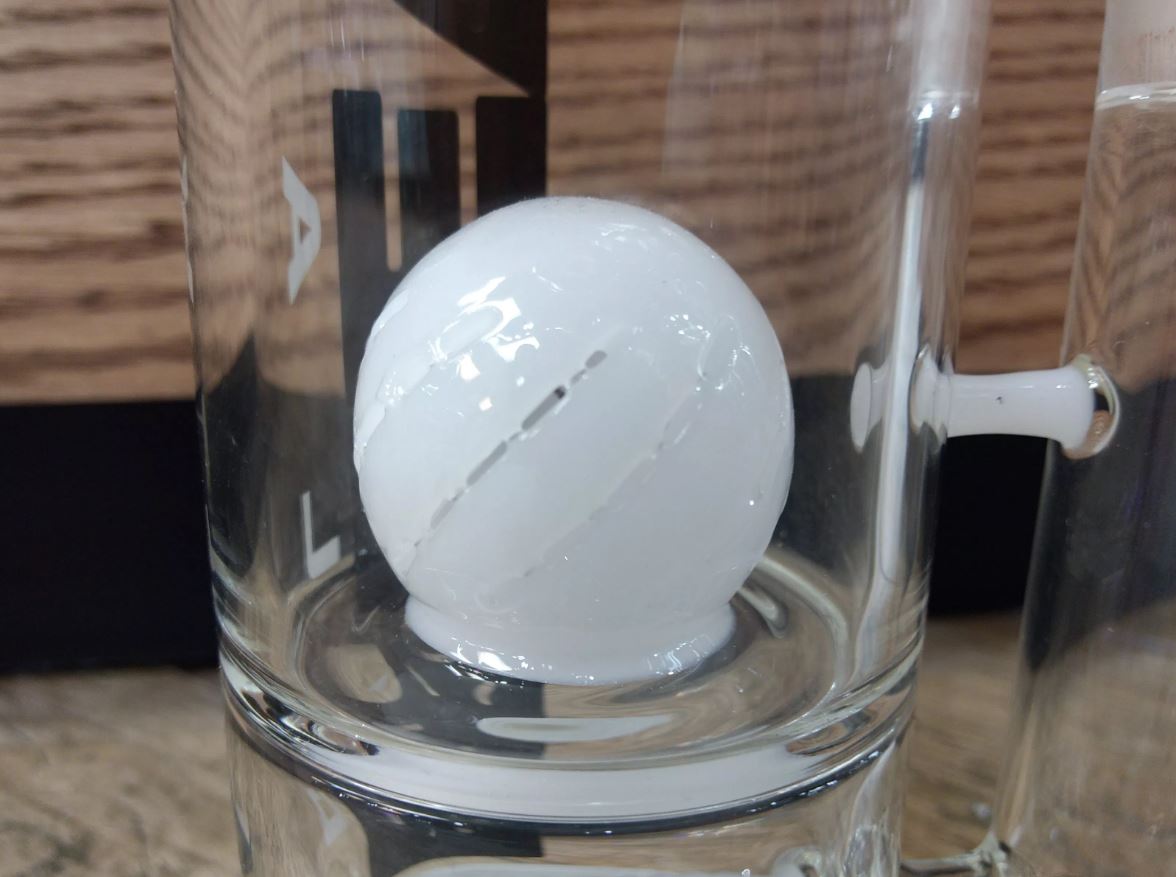
Back to Top
Beaker Perc -
This is a percolator in the shape of a beaker bottom. The blower makes this shape, then he/she will cut slits in the bottom and then weld it into the water pipe or rig.
Back to Top
Downstem Perc -
This is usually the only perc a water pipe gets when its simple. This diffused downstem is made with many small holes. This will make many small bubble that has the vapor or smoke touching more surface area to clean and cool the hit better.
Back to Top
Fountain Perc -
This perc usually sits about the main body and sometimes they stack these, I have seen up to 4 tall in sections. Many many slits to diffuse even more and make small fine bubbles. This is an example of one an artist did.
Back to Top
Inline -
Invented by HopsGlass many many moons ago. This is kinda the start of all the perc rage.
Back to Top
Inline with Slits -
This is a modern inline perc that has slits and then then blower comes back and puts tack welds in the slits to diffuse the air more.
Back to Top
Honeycomb Diffuser -
These are basically a disc with as many as 100 or more holes and these are made in a mold. The tiny holes make tiny bubbles when forced through the Honeycomb Diffuser. This increases the amount of interaction between smoke and water. These are a solid choice, and are extremely popular. We love these! They are durable and diffuse so so well!
Back to Top
Frit Disc Diffuser -
This type of Diffuser bounds tons of tiny glass fragments called frit together leaving tiny holes in between each fragment. The amount of diffusion on a frit disc is pretty much unbeatable. The smoothness of a frit disc diffuser delivery is unparalleled. One thing we see bad about these is they clog very easy as they perc holes are so so small.
Back to Top
Shower Head Perc -
These percs feature slits or holes in order to increase diffusion and filtration. These can range from 3 slits to 50 slits or more.
Back to Top
Spread-Shot Diffuser -
OUT OF CONTROL is what this design is. Takes a long time to make but the function is great!
Back to Top
Tree Perc -
Tree percs offer a great level of diffusion. The more arms they have the more holes there will be and the more percolation you will get. Each of the arms of a tree perc will usually have slits in the side and either a closed or an open bottom, we like them best when each arm is welded to each other. DO NOT BUY if the arms are not welded to each other. A hit and those arms could break off. The smaller the slits, the more the diffusion and filtration.
Back to Top
Single Stem Perc with Slits -
This is one of the most common percs. They work great and are simple and durable. These percs can be made from 1 cut to as many cuts as a blower can cut and put on the percolator.
Back to Top
Vortex Diffuser -
This is a disc that is cut at angles. The angles allow the vapor or smoke to swirl inside the water pipe. Many believe this vortex helps to enhance the flavor as it allows more particles to stick to the side of the glass.
Back to Top
Pick (Rake) -
A rod of metal that has a point ground on it. Used to press into the glass.
Tungsten Pick - This amazing tool is used to move or sew small amounts of heated glass and is most often used to help close small openings found during glass repair or fabrication. One really neat thing that can be done with this tool is that you can slightly heat your glass. Then with just the pick going in and out of the flame (not to heat it too much) so it is red hot but not melting you can push it threw hard glass.
Back to Top
Pi Divider -
A Pi Divider is a mechanical calculator that determines the size of a post needed to pick up a number of canes. The canes are then lain out on the plate and then measured with the straight arms of the Pi Divider. The curved end will indicate the size of the post.
Back to Top
Pipe Cooler -
As the blowpipe is used, heat travels up glassblowing pipes and punties. The pipe cooler sprays water onto the pipe to cool it. It is important to keep the pipe turning when using the pipe cooler or the pipe could warp. Pipes should be cooled from the cool part first and then up towards the moil.
Back to Top
Pistol Grip Glass Cutter -
This tool is used to cut sheets of glass. Many blowers will use this to cut sheets of dichroic glass. This tool features a self-lubricating cutting wheel. Cutting oil is a good thing for these and that is why they are designed to be used with the oil. The oil helps to make a cleaner cut.
Back to Top
Point
This is a tube of glass pulled down from a larger tube. As you pull the piece of glass off the large tube you pull basically a handle for later. This is the start of a pipe or many things.
Back to Top
Powder-
Finely ground glass that is a powder.
Back to Top
Preheating-
The process of heating a glass piece from room temperature to a state sufficient to prevent serious shock when plunged into a flame. This can either be done in a kiln or in the backwash of a flame.
Back to Top
Pre-Mix Burner-
Any burner that mixes the gases inside the body of the burner prior to ignition.
Back to Top
Propane Tank -
This is the tank that holds your fuel called propane, just that simple. They come as 20 and 40 gallon set ups that you can easily get at a Home Depot, or you can go much larger to 1000's of gallons. We use 4 at a time in a bank at our Elev8 Premier studio with 2 of these sets.
Back to Top
Propane Regulator -
This device lets the oxygen run at a nice steady level so the flame works consistently. Mostly it will be used to lower the pressure and keep it steady. Many times if using a K tank or dewar tank the pressures can be 300-2000 PSI. Our GTT torches run on 12 PSI
Back to Top
Punty-
A temporary glass handle to hold the glass for working it.
Back to Top
Quartz Glass-
See Fused Quartz for definition and video
Back to Top
Rack -
This is a tool that is used to store parts. These parts can be tool, prototypes, samples or really anything. Racks are great as they use vertical space in small floor footprint.
Back to Top
Ratachello-
A very unique pattern made in glass that has many lines that cross over each other. The more lines the harder it is to make.
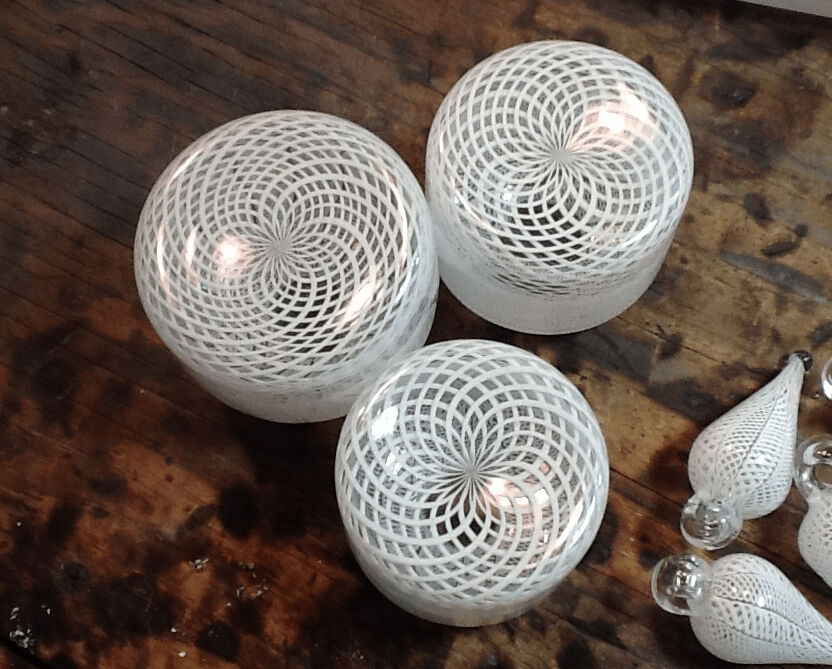
Back to Top
Razor -
An instrument with a sharp blade or combination of blades, used to remove unwanted hair from the face or body. Used to make thin lines in molten glass.
Back to Top
Reducing Flame-
This is the flame with low oxygen. It has a yellow or yellowish color due to carbon or hydrocarbons which bind with (or reduce ) the oxygen contained in the materials processed with the flame. The reducing flame is also called the carburizing flame, since it tends to introduce carbon into the molten metal. This is a cool flame compared to the neutral flame 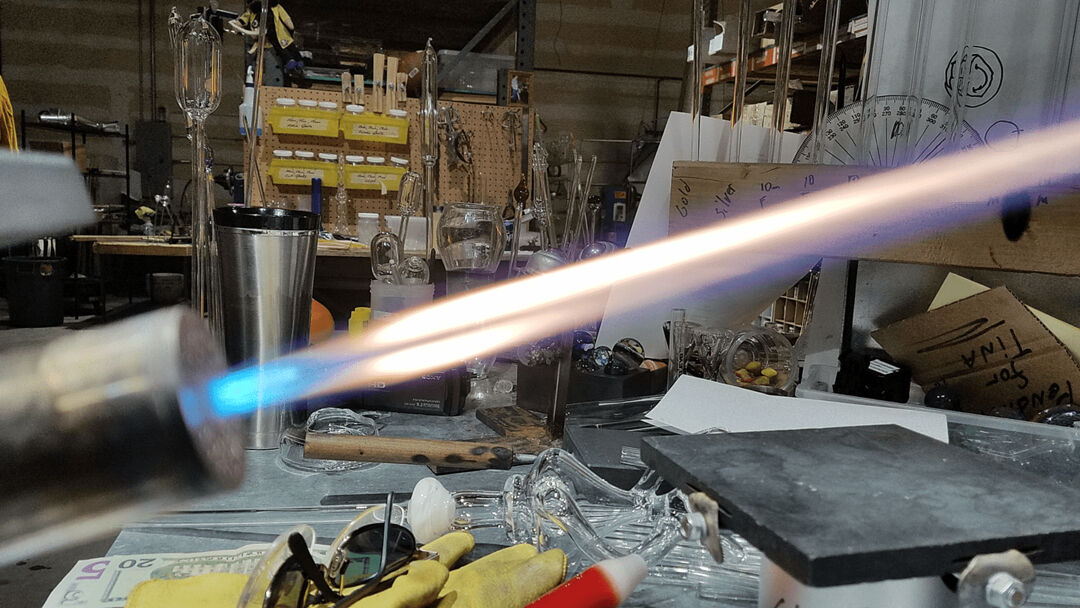
Back to Top
Reamer -
This wonderful tool (a must have in any studio) can be made from metal (usually brass) and graphite. Usually, it is a long point and is made by grinding down 8 sides sometimes 6 sides. It can also be smooth. We prefer octagonal.
Back to Top
Respiratory Hazards-
Melting glass in a flame produces a number of gasses and vapors that can affect your health. It is important, therefore, to ventilate your work area. At the very least, you should provide “dilution ventilation”, in which a steady stream of air flows across your work area, drawing any vapors or gasses away from your face and out of the room. Windows at opposite ends of your work area, one of which has an exhaust fan, can be an effective form of dilution ventilation. Ideally a window should be open behind, or to your side, to ensure fresh air flow. Some lampworking operations may require “local exhaust ventilation,” such as a fume hood, to eliminate hazardous or irritating vapors and gases. If you find that you feel slightly short of breath or that you have a headache at the end of a work session, then you can be certain your ventilation is inadequate. An additional respiratory hazard is posed by glass dust particles you might encounter in your studio or work area. These include powdered “bead release” compounds, the dust stirred up when you work with vermiculite and loose particles of refractory materials such as brick or ceramic-fiber insulation inside your kiln, and especially dust present in frits and powders, or created from cutting, breaking, sanding, grinding or cold working color rods. Dust should be handled with proper safety procedures, including wearing a full tight fitting style, NIOSH certified respirator, with a P100 rating on the cartridge, any time you are creating, or working around glass dust. You do not want to inhale or ingest any glass dust. Take care not to inhale these irritating and potentially harmful dust particles. Be aware of hazardous dusts that can be stirred up when you are cleaning your studio. You can also use a sweeping compound made for fine particulates, in order to keep the glass dust from rising up off the ground. Wet down any questionable areas or spills with a spray bottle before wiping with a wet rag, to reduce the chances of inhaling particles. If you sandblast your finished pieces, follow all safety guidelines appropriate to sandblasting.
Back to Top
Ring Tool (Ring Mold) -
The marvel of marbles is now made significantly simpler. To make a sphere, just grab your trusty Ring Tool or Ring Mold and run it around the bit as it rolls back and forth on the bench. After a few passes, you'll have a new perfect marble. This is works much like a marble mold.
Back to Top
Rod Holder -
A metal rod with an and that will except for a rod of glass. There different styles available, you will have to find what you like and what works best for you.
Back to Top
Rod Rack (Tool Holder) -
A device used to hold your hot glass tips off the bench so they do not cool too fast and crack. You can also rest your tools on there as well.
Back to Top
Rollers (Bench Rollers) -
A device used to hold a tube or rod of glass.
From a glassblower's points of view - So this can help you become a human lathe. The yoke style or rollers with just two rollers are used more for holding rods or tubes while you work the glass. The rollers that have rows or rollers or are just a long roller are mostly used for when you are using a mold. Elev8 Premier uses the rollers with rows for making our ground glass joints.
Back to Top
Rolling Yoke -
A rolling yoke is a necessity when making larger scale or heavier pieces. The gaffer can move the yoke towards the glory hole as needed to help manage the weight of the piece.
Back to Top
Rondelle
A disk of glass formed by spinning and flattening an opened bubble.
Back to Top
Safety System -
Modern studios add safety system to the combustion train of each piece of equipment. The safety system shuts off the equipment if any sort of fault is detected. There are shutoff valves that activate if the gas pressure is too low, too high, or if the flame goes out.
Back to Top
Sandblaster -
A machine that uses air pressure to shoot sand out of a nozzle and onto the piece you are working on. Not always do you really use sand. Here at Elev8 Premier glass studio we use aluminum oxide. This is the standard today. When you use this machine you will want to wear a respirator just encase and sand, aluminum or glass dust escapes.
Back to Top
Scientific Glass-
Scientific Glass is borosilicate glass that is made thick with specific shapes, to make glass that is durable, as well as very clean looking. Scientific Glass often includes complex and enamoring percolators, a well defined shape similar to what a scientist would use in their lab, and an overall uncolored, pure style.
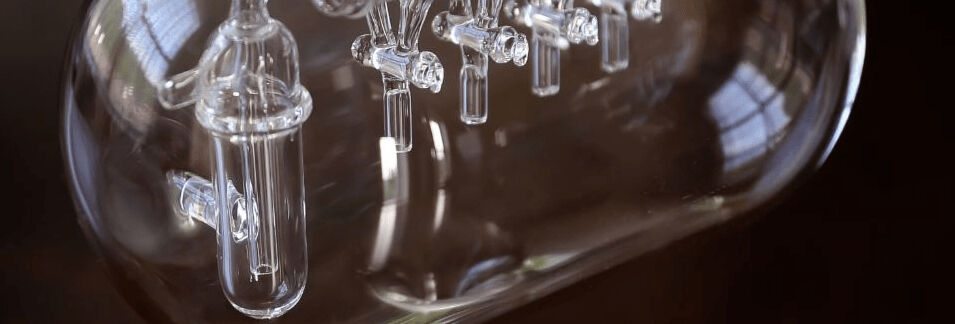
Back to Top
Scavo-
A processes where a corrosive chemical is added to the surface of hot glass while cooling to give the surface a rougher mate finish.
Back to Top
Scoop -
A small spoon to scoop frit from a container and then pour it into the glass you are going to work. Most scoopers are made by the blower and have a pouring end to help the frit pour more directly.

Back to Top
Score-
This is when you take a scoring knife or diamond wheel and cut into the glass. This small scratch or cut on the glass makes it so much easier to break the glass, and break it in a clean pattern. There are many different kinds of score tools to help with cracking glass just right.
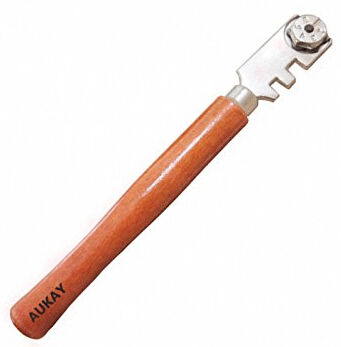
Back to Top
Sculpting Tool -
This is a tool not used in the flame, or very very rarely, so I would say it is not. These can be from picks, to knives, to presses. Really any kind of tool that is used for sculpting is a sculpting tool.

Back to Top
Seed-
Small rock, mineral, kiln part or unwanted bubble that is in the glass. Bubbles are not really seeds, and if you have a seed you should remove it.
Back to Top
Shard-
Glass fragments usually colored of which would be rolled or melted into a working piece for the additions of colors of textures is not melted all of the way. different colors melt at different temperatures lending creative textures with variation.
Back to Top
Shears-
Glassmakers scissors that are used for the cutting, trimming and shaping of hot glass. Usually very primitive in design with heavy gage steel.
Back to Top
Shield (Blast Shield) -
A heat barrier. We LOVE the Blast Shield! This piece of glass in between your flame, work and you will dramatically reduce the heat making your life better
Back to Top
Sifter -
Used to sift crushed glass. Many glass companies will crush the glass into frit with a frit crusher, then they sift it with different mesh sizes to get you what you want for you work.
Back to Top
Silicon-
Silicon is the eighth most common element in the universe by mass. Over 90% of the Earth's crust is composed of silicate minerals, making silicon the second most abundant element in the Earth's crust (about 28% by mass) after oxygen. Most silicon is used commercially without being separated, and often with little processing of the natural minerals. Such use includes industrial construction with clays, silica sand, and stone. Silicates are used in Portland cement for mortar and stucco, and mixed with silica sand and gravel to make concrete for walkways, foundations, and roads. They are also used in white ware ceramics such as porcelain, and in traditional quartz-based soda-lime glass and many other specialty glasses. Silicon compounds such as silicon carbide are used as abrasives and components of high-strength ceramics.
Back to Top
Silicone-
Polymers that include any inert, synthetic compound made up of repeating units of siloxane, which is a chain of alternating silicon atoms and oxygen atoms, frequently combined with carbon or hydrogen or both. They are typically heat-resistant and rubber-like, and are used in sealants, adhesives, lubricants, medicine, cooking utensils, and thermal and electrical insulation.
Back to Top
Silicosis
Silicosis is a lung disease caused by breathing in tiny bits of silica, such as those that within glass. This is a major hazard when sandblasting or crushing frit, that should be addressed by wearing an OSHA dust mask rated for hazardous abrasive particles. Over time, exposure to silica particles causes scarring in the lungs, which can harm your ability to breathe.
Back to Top
Silveria-
A type of art glass with encased silver foil
Back to Top
Sleeving-
Sleeving is a glassblowing technique where a blower incerts a tube into another tube and then removes all the air between the two tubes. This is used for alien skin, encasing millies on a tube, or putting one color inside another so a person can grawl and get differnt colors from the depths.
Back to Top
Slumping-
Slumping glass is a highly technical operation that is subject to many variations, both controlled and uncontrolled. When an item is being slumped in a kiln, the mold over which it is being formed (which can be made of either ceramic, sand or metal) must be coated with a release agent that will stop the molten glass from sticking to the mold. Such release agents, a typical one being boron nitride, give off toxic fumes when they are first heated and must be used in a ventilated area. The glass is cut to the shape of the mold (but slightly larger to allow for shrinkage) and placed on top of it, before the kiln is heated.
Back to Top
Soak-
To keep glass at a specific temperature for an extended period of time, such as annealing
Back to Top
Soap -
We use this to find leaks in our lines. We will a bottle of part soap like Dawn and part water. Spray this on any connection you make to guarantee you have no leaks.
Back to Top
Soda-
Sodium Oxide (Na₂O), or common used by glassblowers in first Reference to Sodium Carbonate (Na₂CO₃)
Back to Top
Sodium Flare-
The bright light that is given off of the reaction of oxygen rich flame and the sodium of the glass in a kiln. didymium glass in the glasses to avoid serious damage to the vision of ones eyes. usually, flame-workers lamp-workers are at the primary concern here.
Back to Top
Soft Glass-
The most popular glass for lampworking is soda-lime glass, which is available pre-colored. Soda-lime glass is the traditional mix used in blown furnace glass, and lampworking glass rods were originally hand-drawn from the furnace and allowed to cool for use by lampworkers. Today soda-lime, or "soft" glass is manufactured globally, including Italy, Germany, Czech Republic, China and America.
Soft Glass by a blower - This is a lot of things in glass really. They are most all the glass, bottles, high color water pipes, those big dishes, things that Dale Chihuly does.
Back to Top
Sophieta -
This tool is used to inflate a vessel after is has been removed from the blow tube. Many times the piece is then attached to a punty so that the blower and work the glass. As the vessel heated, the conical nozzle of the sophieta is inserted into the vessel's mouth so that the blower can put pressure into the glass object he/she is working on.
Back to Top
Spray Bottle -
We use to fill with soap, Windex or CLR to clean things.
Titanium Pen by a glassblower - This is a valuable tool for all kinds of things. You need one filled with saop to find leaks. You need one filled with windex or a glass cleaner to clean your glass. You need one filled with bathroom cleaner to keep that bathroom tidy.
Back to Top
Strain Point-
The strain point is defined as a temperature at which a certain glass viscosity is reached. It is that point at which all movement of the glass molecules has reached a point at which no more strain can be introduced into the hot glass. It is usually about 100 degrees F or so below the annealing temperature. Like all such temperatures it represents some point in the range of such temperatures for a glass family. For example, for Effetre/Moretti glass the annealing temperature is usually listed as 968 degrees F and the strain point about 840 degrees F.
Back to Top
Stem -
The stem connects the foot of a goblet to the bowl. This is a traditional chicken-leg shaped stem. Most of the creativity in Venetian goblets is expressed in the stem; animals, flowers and fancy bitwork are common.
Back to Top
Stopper -
These are used to plug tubes. They are also used to allow your blow tube to hook up to your glass tube via a swivel.
The difference between stoppers - Multi-stoppers are manufactured of red silicone rubber and green neoprene. The rings are cut from the same stopper, each ring fitting perfectly inside the next. This allows for vacuum-tight fit for all openings within a stopper size range. Ideally suited for glass working operations and chemistry labs. Multi-stoppers made of red silicone rubber are suitable for higher temperature applications with a serviceable temperature range from -100F to +450F. These stoppers are resistant to hot oils, fuels, oxidizing chemicals, sodium hydroxide, and ozone. Multi stoppers made from green neoprene rubber have better aging characteristics than those of natural (black) rubber and are resistant to oils, solvents, ozone, and hydrocarbons. The serviceable temperature range is from -40 Degrees C to +100 Degrees C.
Back to Top
Stress-
A force exerted on a material, such as the internal stress inside glass caused by uneven heating.
Back to Top
Striking-
Striking colors are glasses that can be 2 different colors. It has to do with the orientation of the molecules inside the glass, which will change from one state to another on being cooled and re-heated. Transparent reds, oranges and yellows and most opaque pinks, for example, are striking colors. Usually you strike colors at the last step after shaping a bead, by letting the glass cool and reheating it quickly in the flame so that it takes the shade you want it to be. By Henry Grimmett
Some glass formulations, such as transparent ruby (colored with copper) and those that are colored with silver, change color when heated or cooled in specific ways. However, the reasons for their color changes aren't necessarily the same. The term striking has come to refer to any color change in the glass due to heat treatment of some sort. While this terminology is acceptable for lampworking it should be understood that copper and silver glasses undergo very different reactions.
In our Ruby glasses copper is the element responsible for the color change. Copper oxides (Cu2O) are added to the batch and melted. As the glass is melted the Copper molecules and the associated oxygen molecules break apart and join with other molecules in the batch. Rapid cooling of the glass causes these high temperature bonds to become permanent and leaves the glass clear. The magic of the ruby color is that these bonds can be broken at the annealing temperature of the glass and the copper is free to create Cu2O and colloidal Cu particles. (There is some debate whether it is the Cu or the Cu2O that creates the ruby color, however, a combination of the two creates the best effect). Glasses that undergo this type of molecular realignment are what were traditionally referred to as striking colors.
The other type of color change is caused by crystal growth. Glasses such as our Silver Strike series, our Amazon series, and our Chameleon series, can be looked at as having millions of tiny molecules of silver floating around the glass network. These tiny silver particles reflect a yellow wavelength when evenly dispersed through the glass. The fundamental difference between the copper and silver strike is how these particles react to heat. The copper particles free themselves and form individual Cu or Cu2O particles that reflect red light. The more red particles there are, the darker the ruby color. Silver, however, frees itself from the glass and bonds with other free silver particles creating silver crystals of varying size.
The crystal growth process is a function of time and temperature, and can be controlled for the creation of the full spectrum of colors silver can produce. If the glass is subjected to high heat, the silver particles are freed from the glass matrix and move through the glass until subsequent cooling forces them back into the matrix causing the glass to look the same as before it was heated. (Note: Returning to its original rod color takes place in glass that contains only silver. Glasses such as the Amazon and Chameleon series, have nuclei present which allow silver particles to form crystals and prevent them from returning to their original state.) When the glass is cooled, not all of the silver particles make it back into the glass matrix. Upon subsequent heating these homeless silver bits act as nuclei, or places for larger, more stable silver crystals to grow. It is this heating, cooling and reheating process that enables larger crystal growth. The color reflected by the glass is a function of the size of these crystals varying from yellow (small crystals) though purple, blues and greens (large crystals).
Back to Top
Stringer-
This is a small rod of glass that is pulled down to be very fine. Maybe about .5 mm-5 mm thick. These are used for drawing lines on things or used for ratichilios, fillichelios and just those cool lines on inside out work.
Back to Top
Stump Sucker -
The Stump-sucker is a very neat and clever tool. Its a very simple and inexpensive graphite tool that uses suction to encase objects in clear glass.
How it works: the object is placed in the graphite chamber, heated with a torch, and then covered by a molten mass of clear glass. Using the hose with mouthpiece, the artist becomes the vacuum pump, sucking through the hose to pull clear glass around the object being encased.
Back to Top
Switch Ball
This can be a lot of different piece of glass that are switched from one axis to the other. This will give you two terminations. Many times this is made on line worked tubing to give that wig wag effect that is just so freaking amazing!! This is a very complex piece of glass. Sometimes this is called switch axis because you are switching the axis of the glass. This piece of glass starts sometimes with a 50mm to 80mm piece of clear tubing lined with stripes of glass. It is then sleeved with more clear glass, or striped with clear glass, to make more colored glass. This becomes a large colored tube of glass. This large tube is pulled down to a 10mm-20mm diameter tubing, cut in 2-5 inch lengths. Then wigwagged back and forth to make a wig wag effect. Some blowers will use the benderback technique. One end is terminated and the tube is then turned to a ball of glass. A hole is (popped) 90 degrees from the termination to then switch the axis. Next, the other end is terminated and you have a switch ball. This can take roughly 2-3 hours to make 10-15 switch balls, or approximately 10-15 minutes per switch ball. The cleaner the ball the longer it takes to make.
.
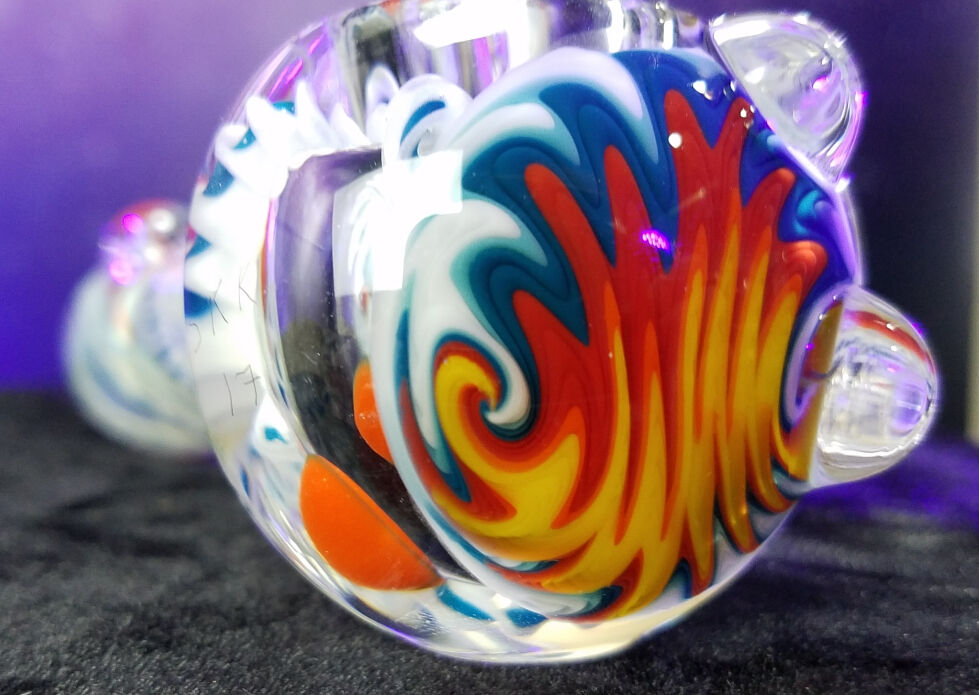
Back to Top
Swivel -
This tool is used with a blow tube and usually some kind of a plug like a cork, silicon or rubber style. This allows the blow tube to not kink up from spinning the glass.

Back to Top
Tanks-
Potential hazards also exist any time you work with compressed gasses. Carefully follow any manufacturer’s instructions that come with your regulators or gas tanks and check with your suppliers for safe operating procedures. Never move oxygen tanks without their protective cap in place. If the tank falls over, the valve stem can be sheared off by impacting against a table or other object. The pressure inside the tank may then be high enough to send the cylinder flying like a rocket, injuring you and damaging your building. Oxygen tanks should be either laid on their side and secured to prevent rolling, or chained securely to a wall so they don’t fall over. Note also that oxygen regulators, hoses and fittings should never come into contact with grease or oil, which can ignite spontaneously in the presence of pure oxygen. Be sure to install check valves and flashback regulators on your fuel, gas and oxygen regulators to prevent backwards flow of gasses-a major hazard in the event of a fire or torch malfunction. Make sure that your torch is secured to the work surface so that it doesn’t move if a hose is yanked. Keep all flammable and combustible materials well away from your torch. At the end of each work/play day, shut off your oxygen and gas tanks and bleed the pressure out of the lines by opening your torch valves.
Back to Top
Tape Measure -
An instrument used to get measurements. In the USA most are done in AS (we call inches). But now a days you can find them that read both AS and Metric.
Back to Top
Termination-
A glass termination is where the glass is closed up and the opening becomes closed. When done properly the glass termination will look like all the colors come together in a tight point. In a bad termination the point where the colors come together will look fuzzy, color boils can happen and it will just not look on point. Terminations will be found on colored tubing when turned to a switch ball.

Back to Top
Thermal Coefficient of Expansion-
Also: COE, LCE, α (alpha); The relative amount by which a material will expand per degree when heated. The smaller the COE, the more resistant the glass is to thermal shock. Expressed as an exponent, Borosilicate's COE is ~3×10⁻⁶ K⁻¹ at 20°C
Back to Top
Thermal Shock-
The strain created by abrupt heating or cooling.
Back to Top
Thermocouple-
An instrument that is a bi-metal probe that measures the kiln temperature by means of resistance.
Back to Top
Thermometer-
An instrument for measuring and indicating temperature.
Back to Top
Tile Saw (Wet Saw) -
This is a machine that holds a diamond blade used to cut very hard materials such as tile and glass. These are best to always run with water to keep the dust down and to keep the blade and material cool as it is cut. The finer the grit on the blade, the finer the cut will be. Some blades are so clean they do not boil when you fire polish them.
Back to Top
Timer -
We use this to keep track of how long a project takes us. If you do not know its hard to know if you are improving, or what to charge. We have one of these at each station.
Back to Top
Titanium Pen-
A piece of metal ground or filed to a point. Titanium Pen by a blower - This used to sign a blowers art. The glass must be wet to write with the piece of metal. It leaves a mirror like signature when used properly.

Back to Top
Tongs-
There are used to grab and hold hot glass. They are basically normal cooking tongs, but wrapped with some fiberglass to keep from scratching the hot glass.
Back to Top
Torch (Hand Torch) -
An open flame for heating up glass directly.
Torch explanation by a blower - This is the thing that gives us the fire and allows us to melt the glass. There are tons of torches out there. First a blower in this industry needs a bench top torch, then a great addition is a hand torch for getting in all the places you can not get to with a bench torch.
Hand Torch - This is a little smaller torch a blower uses while they are holding the torch in their hand. Hense the name hand torch.
Torch Brands: GTT-Carlisle-Nortel-National-Bethlehem-Herbert Arnold
Back to Top
Tweezers -
Special tongs for glassblowing that are long, wide-spread, and have bent tips for fine gripping.
Standard Tweezers by a blower - These are used for grabbing bits of glass whether molting or hard.
Peter Tweezers by a blower - These tweezers are great for making loops and holes for pendants, vessels and buttons. To make loops and holes: place a small amount of glass shaped like a tall bump at the desired location. Heat up just the bump to just shy of it melting down. Quickly place the points of the tweezers to the center of the heated bump and squeeze together. As soon as the tips touch, move the handle back and forth a couple of times in a motion that makes the points rotate in the center of the hole. This motion breaks apart the fine web that would otherwise bridge across the middle of the hole. Remove the plyers and reheat the glass area making up the hole, being careful not to melt the hole closed. Again place the tweezers in the hole and stretch out the hole to the desired size and shape. To make a large loop, simply start with a larger bump of glass. You may also need to reheat more than one time. For a wider loop, start with a bump that is slightly oval shaped at its base.
Squeezer Tweezers by a blower - These are used to open holes further without smashing the glass, but stretching it out rather.
Hemostat Tweezers by a blower - These are used to grab marbles.
Back to Top
Twisty Cane-
A piece of rod or cane that has been twisted to give a candy cane effect. Twisty Cane by a blower - There are a few ways to make a twisty cane in glass blowing. One method is to take a clear rod, maybe 10 or 8 mm. Then take some colored rods and trip the clear rod. Heat it up allowing the colors to melt to one piece and get it like a foot ball. Then pull it and twist it to a cane or stringer. A second method is to take the colored rods and bundle them how you wish the colors to go. Then melt to a 10mm or lager rod and melt into a foot ball again. Then pull and twist into a cane or stringer.
Back to Top
Uranium Glass
Uranium glass contains Uranium, and emits low levels of radiation. Like any borosilicate color, it should be handled with proper safety procedures, including wearing a full tight fitting style, NIOSH certified respirator, with a P100 rating on the cartridge, any time you are creating, or working around glass dust. Like dust from any borosilicate color, you do not want to inhale or ingest any dust. In addition, we recommend you do additional research, in addition to the resources referenced below, to learn about long term low level radiation exposure, especially in cases where this glass will be in close proximity to a person, like wearing a pendant. More information on uranium glass can be found here: https://www.orau.org/ptp/collection/consumer%20pr... References Buckley et al. Environmental Assessment of Consumer Products Containing Radioactive Material. Nuclear Regulatory Commission. NUREG/CR-1775. 1980. Landa, E. and Councell, T. Leaching of Uranium from Glass and Ceramic Foodware and Decorative Items. Health Physics 63 (3): 343-348; 1992. Nuclear Regulatory Commission. Systematic Radiological Assessment of Exemptions for Source and Byproduct Materials. NUREG 1717. June 2001.
Back to Top
UV Flash Light -
This is a flashlight that emits ultra violet light. We have found the best nano-meter wavelength is from 365 to 380 to see UF reactive glass.
Back to Top
UV Reactive Glass-
Glass that when UV light is on it changes. This glass can be one color outside or under florescent lights, but when you put it in the dark and put pure UV light on it, WOW it glows way different than it did in the light. Below are what is kinda on the market now. The market is always growing with new colors coming out near-weekly. We have found the best nano-meter wavelength is from 365 to 380. Green - Many people call this Illuminati as North Star was one of the first to bring it to the borosilicate art glass world. This glass has radioactive uranium dioxide in it. This glass is light green or yellowish in plain light, but POPS bright green under UV light.
Blue - The first we seen bring this to the market was Trautman Art Glass called Blu-V. These are trade secrets from what we know of what goes into these. But we think maybe it is fluorite as it glows blue/purple. Pink - Lucy was the first we seen on the market by Northstar . Again, we do not know what its made with but we think it is Calcite.
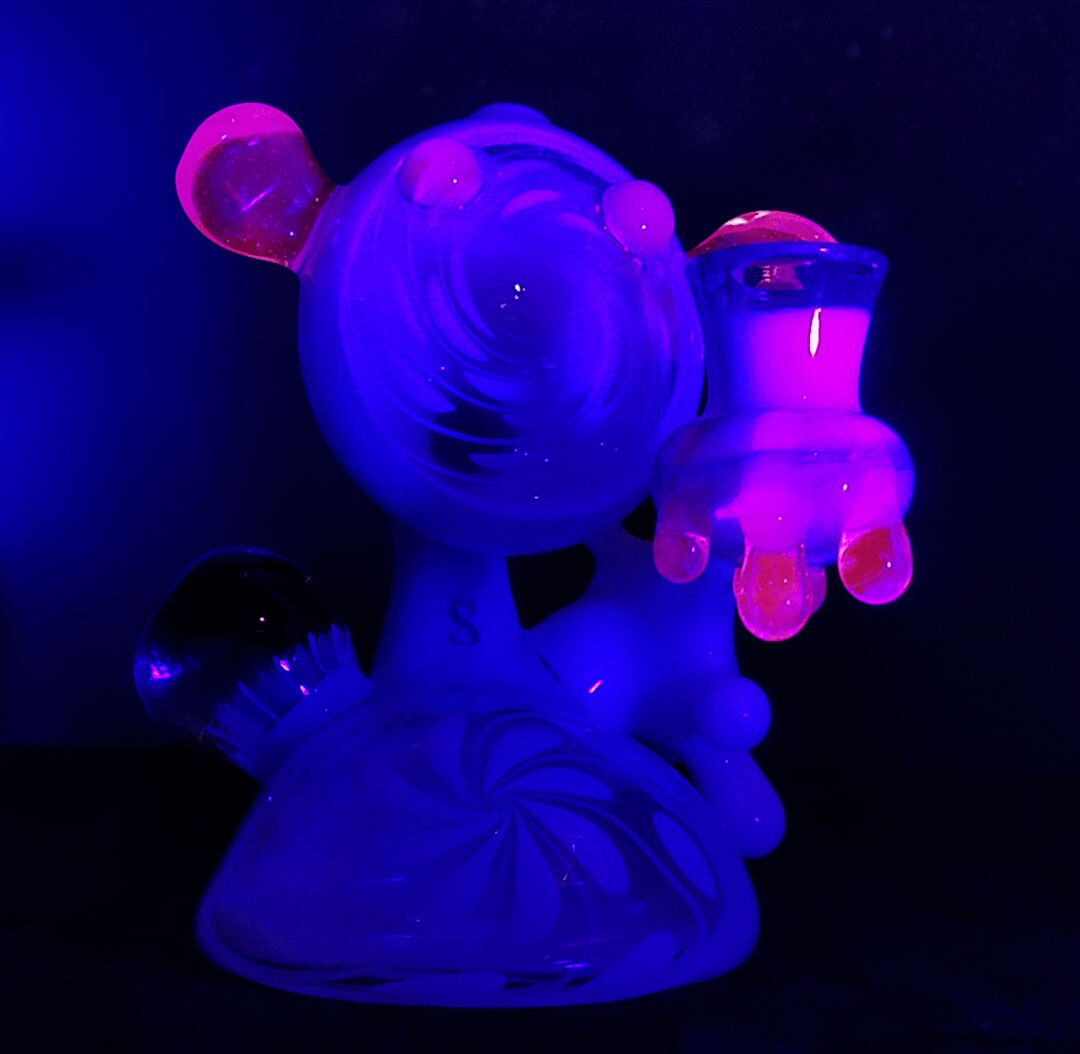
Back to Top
Veri-Flame -
This is the brain that controls the safety system. The Veri-Flame system is the standard used at most glass studios, though there are other manufacturers. Veri-Flames are relatively simple and economical.
Back to Top
Vermiculite -
A hydrous phyllosilicate mineral. It undergoes significant expansion when heated. Exfoliation occurs when the mineral is heated sufficiently, and the effect is routinely produced in commercial furnaces. Vermiculite is formed by weathering or hydrothermal alteration of biotite or phlogopite. Large commercial vermiculite mines currently exist in Russia, South Africa, China, and Brazil.
Vermiculite by a blower - This stuff is used to let the glass cool slower than sitting in the air. This is for say small marbles that you do not want to anneal in the kiln. You can get away with this method of annealing, but in a kiln is best.
Back to Top
Vice -
A metal tool with movable jaws that are used to hold an object firmly in place while work is done on it, typically attached to a workbench.
Back to Top
Viscosity-
A fluid is a measure of its resistance to gradual deformation by shear stress or tensile stress. For liquids, it corresponds to the informal concept of "thickness"; for example, honey has a much higher viscosity than water. Viscosity is a property of the fluid which opposes the relative motion between the two surfaces of the fluid that are moving at different velocities. In simple terms, viscosity means friction between the molecules of fluid. When the fluid is forced through a tube, the particles which compose the fluid generally move more quickly near the tube's axis and more slowly near its walls; therefore some stress(such as a pressure difference between the two ends of the tube) is needed to overcome the friction between particle layers to keep the fluid moving. For a given velocity pattern, the stress required is proportional to the fluid's viscosity. Viscosity by a blower - This how the glass gets liquid. Clear has no other elements making it the thinnest or runniest of glass in the boro world. The more saturated a color is the higher the viscosity is. This becomes very apparent when a blower makes lined tube work with a high and low viscosity color. The low viscosity colors will kinda condense and pull together. The blower must learn to work this properly such as if it was half black and half white, the blower may do 8 lines black and 10 lines white. When worked they may end up looking like they had the same amount of lines for the color.
Back to Top
Wet Room-
This is a dedicated room where a blower will do cold work that uses water to lubricate as it is cut. Many times you will find a lapping wheel, diamond saw, maybe a drill press with a diamond bit even.
Back to Top
Wetting Off-
The separation line for the glass work from the blowpipe or pipe uses cold water to fracture control the break and separation.
Back to Top
Window-
This is a piece of glass that a blower places in another piece of glass. This make it look like there is a window in the glass. The window can be a switch ball, clear glass, bubble trap or any piece of glass the blower wishes to put inside the glass. Usually the blower must switch the axis of the glass so that the piece of glass he/she puts into the glass is on the side to make a window effect. This is a higher skill set for a blower.
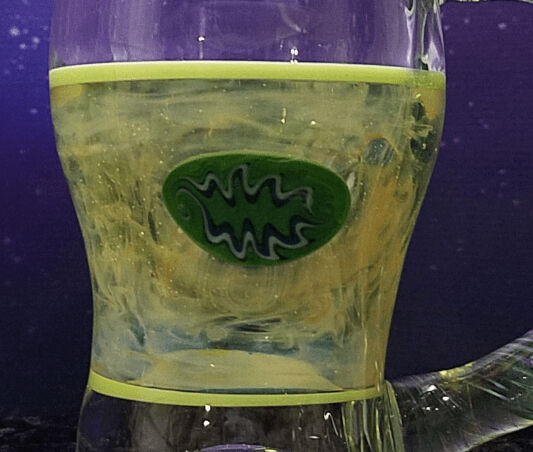
Back to Top
Wood Block -
Used as a great tool to hold your glass. Unlike a brick, you can drill it out how you like. Be careful not to burn it, but if you do a little, it sure smells good? We recommend a larger piece of wood for the weight. The weight is very important. You can also screw these to your table.
Back to Top
Working Range -
This is the temperature range that the glass is able to be worked in while it is soft, or liquid.
Back to Top
Wrap and Rake-
One of the more basic yet when done right can be just amazing! This technique gives the glass like a scallop effect of dragging effect.
Back to Top
Wrap-
- This part of the technique is what will give the underlying pasterns and colors. You will take a warm piece of glass, the hotter the better so the colored glass will stick to it. You can also fume the glass and wrap with clear or any color for that mater. To wrap the glass you must develop a technique of spinning the hot glass while taking a stringer off the clear or colored rod of glass. The faster you spin the thinner the stringer lines, the slower the thicker the stringer lines will be. Once you have it wrapped I like to heat up the color or clear stringers that wrap the glass and paddle them slightly to the glass to make sure they are sticking good.
Rake-
- This is the second part of the technique that will give the wrap the near effect. Mostly I use a clear 5mm rod for this, but you can use nearly any color, while transparents tend to give the best effect. To start the rake process you will pre heat the glass rod you will be using to rake. Then heat up a line on the glass you wrapped. Once you have the line heated you will run the flame at an angle so that you just slightly hit the wrapped glass while pulling the clear through the wrapped glass. This is what make the pulling effect as you will pull the clear through the spun color. Repeat this over and over. You can go close next the the prior rake, or you can go further away. You can even rake towards you, then rake away. There are a ton of things you can do with this technique and never seems to get old.
Back to Top
Wig Wag-
This is when a blower twists lined color back and forth making a say wig wag pattern, hence the name. There are a lot of ways to make this happen, but the ultimate goal is to get that back and forth pattern. One great technique is the bender back way.
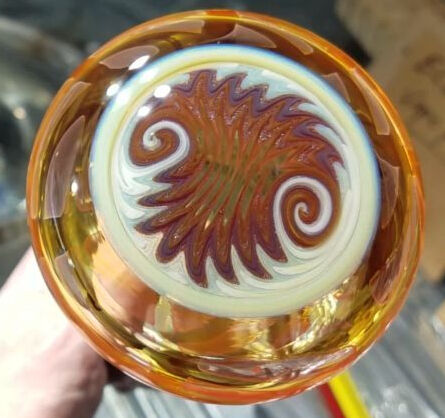
Back to Top
Yoke-
The weight support for the glassworker while in the glory hole while being flashed References
Back to Top
- Wikipedia
- www.mountainglass.com